Factories built much of the world as we know it. Many of the fundamental characteristics of the modern economy were unknown before the entrepreneurs of the first industrial revolution established mills for the large-scale processing of cotton, metal and clay. Mechanization, standardization and the division of labor have gone on to have social and economic effects that would have amazed even those early industrialists.
Over the ensuing 250 years, the idea of the factory has lost none of its power. Today, governments around the world vie to create the conditions in which homegrown manufacturing can thrive, or to entice big global players to establish production facilities on their soil. Everyone wants to play host to the factories of the future. The government of Wisconsin, for example, has offered incentives and subsidies worth a reported $4.1 billion to Chinese electronics company Foxconn, which plans to build a major TV plant in the U.S. state. Further west, the state of Nevada promised tax breaks of up to $1.3 billion to host carmaker Tesla’s “Gigafactory” battery plant. In China, cities such as Dongguan in Guangdong province offer manufacturers in selected industries benefits including cash grants, reduced taxes and free land. Their aim is to encourage the development of advanced industry clusters, and to maintain investment as labor costs rise
Nobody knows, however, exactly what form those future factories will take. Some think nostalgically about the large-scale employment provided by the vast, labor-intensive manufacturing plants of the past. Others have a vision of mass automation, with every task completed, with unerring precision, by an army of robots.
Some believe that advances in technology will undermine the very characteristics that made the factory model so successful. They envision a return to small-scale distributed production, where ultraflexible automated manufacturing equipment allows microfactories to make a wide range of products to order for local customers, a high-tech version of the pre-industrial blacksmith’s shop.
Which of those visions is more realistic? Most probably, tomorrow’s factories will contain a little of each.
Still working
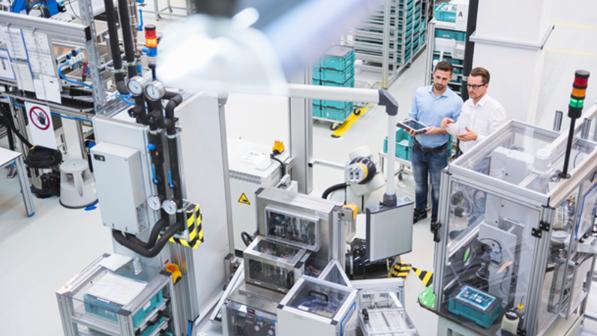
First, take jobs. Decades of rising productivity, driven by a combination of automation and smart management, mean that manufacturing industries need fewer people to produce the same level of output. In mature economies, a return to historical levels of factory employment is unlikely. In the U.S., for example, manufacturing employment as a share of total employment peaked in the 1920s and has been declining ever since. And even the new manufacturing powerhouses of East Asia are looking to automation rather than an ever-expanding workforce to fuel their long-term growth.
Researchers at consultancy McKinsey & Company estimate that, in manufacturing organizations, around 60 percent of the tasks currently completed by people could be automated using technologies that already exist today. Significantly, that number includes activities away from the factory floor, like design and management. McKinsey believes that the technical ability to automate the remaining tasks is likely to evolve by the middle of this century.
That doesn’t mean manufacturing jobs will disappear any time soon. To be adopted at scale, automation must be economically viable and socially acceptable, not just technically feasible. The McKinsey researchers believe that this transition will take 100 years or even more.
The human-machine interface
The vast majority of 21st-century factories will continue to involve collaboration between people and machines. The distribution of tasks between them is likely to change dramatically, however. Digitalization is powering a new industrial revolution, one that proponents claim will result in a step change in speed, quality, productivity and flexibility.
Technological change is touching all aspects of factory life. Robots are getting cheaper, more capable and easier to use, for example. That’s allowing companies to use them outside the relatively narrow range of tasks that they have hitherto dominated
But an even larger transfer of responsibilities is underway behind the scenes. The development of advanced data analytics, some of them powered by artificial intelligence (AI) technologies, means machines are taking increasing responsibility for high-level decision-making in manufacturing: planning production schedules, fine-tuning processes and solving problems.
One company that is positioning itself on the frontline of this “fourth industrial revolution” is U.S. industrial conglomerate Honeywell. Eric Seidel is Vice President of Strategy and Chief Marketing Officer for the company’s Process Solutions business. He explains that improved data connectivity will be a key enabler for the future transformation of manufacturing.
“Today’s factories are generating gigabytes of data, from their processes and production assets and even from the workflows of their people. But that data isn’t yet connected,” he says. “The factory of the future won’t just connect all its data seamlessly, enabling actionable insights and much faster decision-making, it will also extend those connections beyond the four walls of the factory. For the first time, manufacturers will be able to think about the whole supply chain, all the way -upstream into their suppliers and all the way downstream through logistics and into their customers.”
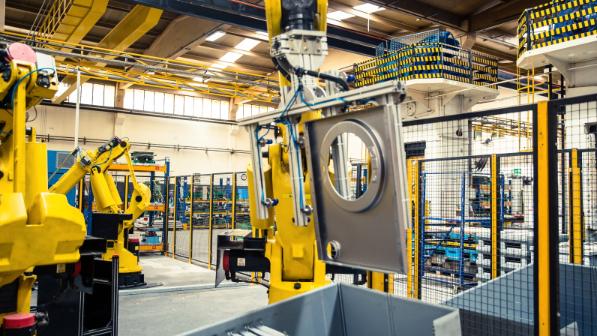
Improved connectivity creates three major opportunities for manufacturers, Seidel continues. “The first is that, across your entire supply chain, digitalization will eliminate a huge amount of the variability that companies have to deal with today: Every day will be your best day of performance.”
The second big opportunity is the use of technology to empower the factory workforce, by providing dramatically improved access to data and information. With the right tools and support infrastructure in place, he says, “everybody on your site can act as a leading expert.” The tools and systems that enable that expertise include advanced training technologies, such as virtual reality (VR) systems and augmented reality (AR) technologies that use smart glasses to overlay information on the workers’ field of view, says Seidel.
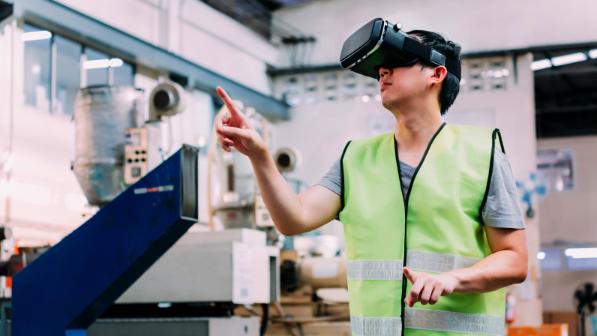
The third and final opportunity, he suggests, is to identify and capture opportunities for further process improvement outside of the plant’s four walls with the help of smart analytics. “Once we are operating so every day is as good as the best day and every employee is as effective as the leading expert, we can start to look across factories and ask ‘how well does the best facility in the world perform?’ Then we can start to use continuous improvement to enhance the output or the throughput of the plant until our performance matches the best that can be achieved.”
Right now, says Seidel, while many of Honeywell’s customers are pursuing this vision of digitally enabled manufacturing excellence, most are only part of the way into their journey. The picture he paints is one of rapid change, however. “Three or four years ago, there was a lot of hype around digital manufacturing. Companies were wondering what these technologies might do for them. There was a lot experimentation and proof-of-concept work going on.”
Today, he says, companies are beginning to employ advanced digital approaches in production, but most effort is focused on individual assets rather than complete factories or supply chains. “We see companies connecting a single pump or chiller unit to a cloud data service provided by the manufacturer of that asset, and they’re getting a lot of insight from doing that.” Those insights might include the use of predictive analytics to optimize energy use or enhance reliability, he explains.
The next step beyond this “vertical” digitalization is for companies to make use of “horizontal” connections, first between the machines in their own facilities and eventually across the supply chain, to supplier and customer machines, facilities and processes. That’s rare today, but it is something that Seidel expects to see “on a much more common basis over the next couple of years.”
Why go looking for the latest logistics stories and insights when you can have them delivered right to you?
What’s stopping you?
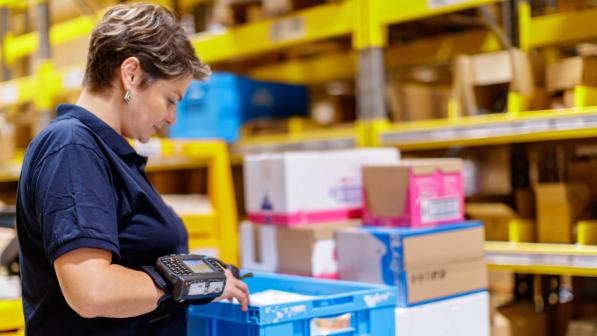
Does that mean the factory of the future could already be here? Technology isn’t the primary barrier to development, says Seidel. “It’s already relatively simple for companies to connect their manufacturing assets to digital networks.” Some companies are still cautious about the idea of shared, centralized data, however, especially when they start to think about systems that are accessible beyond the barriers of their own organizations.
“In our discussions with manufacturing companies today, we come across two related sets of concerns,” he notes. “The first is over cybersecurity, and the second is about the choice of cloud. Do they host their own data, or choose a system provided by an OEM or a third-party partner?”
It’s no surprise that manufacturers want to protect their data. Decades spent incrementally improving the performance of their operations has taught these companies that it’s the small details that can matter most in manufacturing competitiveness. And cyberattacks have already stopped production lines in several plants around the world. Sensitive data isn’t unique to manufacturing, however, and other industries have shown that concerns over data security and availability can be overcome with the right partners and effective management.
What about the workers? Is there significant resistance to digitalization among factory personnel? In practice, Seidel says that implications for the workforce are usually “among the easier discussions” Honeywell has when it talks to customers about digital factory projects. In part, he says, that’s because many companies are already wrestling with skills shortages and an aging workforce. “In the industries we serve, around 40 to 43 percent of skilled labor is going to leave the industry over the next six to eight years. Companies are already trying to figure out how they are going to manage the loss of skills and knowledge as employees who have worked for them for 20 or 30 years reach retirement age.” Against that background, he says, companies may see digitalization as a way to accelerate training and keep know-how inside the organization.
Closing the loop
The factories of the future will require new approaches to logistics too. Digitally enabled manufacturing won’t just enhance efficiency, it will also make production systems far more responsive to their customers, notes Reg Kenney, President Engineering and Manufacturing, DHL. “We are already seeing how customers want faster service and products that are tailored to match their needs. For manufacturers those requirements translate into a far larger number of variants, and far shorter planning, order and delivery cycles.”
As factories become faster on their feet, the rest of the supply chain must do the same. “Speed and flexibility are becoming increasingly critical for our customers across the engineering and manufacturing sector,” says Kenney. “Digital technologies can help here, by improving the way companies share information like demand forecasts, but they also need advanced logistics capabilities to cope with fast-changing demand.” — Jonathan Ward
Published: January 2019
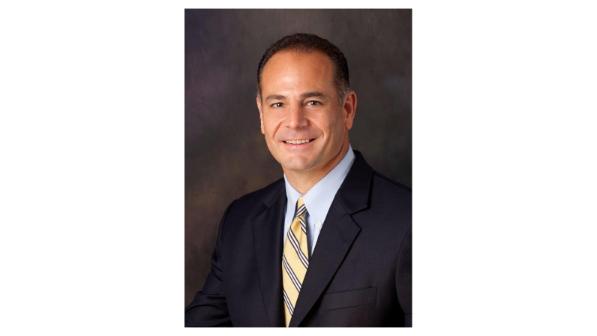
Eric Seidel
is Vice President of Strategy and CMO for Honeywell Process Solutions, a pioneer in process automation control that serves industrial process manufacturers worldwide. Eric leads the global marketing organization and the strategic planning process to deliver overall growth for the business. Prior to Honeywell, Eric was Vice President with Ingersoll Rand holding multiple general management roles over his career and led the Compression Technologies IIoT digital transformation business. He has over 20 years’ experience with industrial end markets, as well as international operations while in private equity in the renewable energy sector.
Images: iStock, Pete Winkel/Honeywell