It’s an activity that predates the first industrial revolution by several thousand years, but agriculture has always embraced new technologies. Today’s farmers operate machines guided by precision GPS systems, and make decisions on the basis of high-resolution satellite imagery and advanced analytics technologies.
For agricultural equipment maker AGCO, high-tech has long been an integral part of its customer offering, but the company is also positioning itself at the forefront of the digital revolution in manufacturing.
A relatively young company, AGCO was formed as the Allis-Gleaner Corporation in 1990 when U.S. managers bought the Deutz-Allis tractor and equipment manufacturer from German owner KHD. The business grew rapidly through a series of acquisitions and AGCO now owns a number of major agricultural equipment brands, including Challenger, Fendt, Massey Ferguson and Valtra. Today, the company has a truly global presence, with 53 manufacturing plants worldwide and sales and support activities in every major market.
Peggy Gulick is AGCO’s Director of Digital Transformation, Global Manufacturing. The role has existed for only a year, but Gulick explains that individual plants have been exploring and applying digital manufacturing technologies for some time. Her job is to encourage the continued development of new digital solutions, and to help plants across the AGCO network to adopt approaches that have proved successful elsewhere in the group.
That’s a model that AGCO understands very well. The company has developed a sophisticated manufacturing philosophy, the AGCO Production System, built on lean principles of standardization, waste reduction, continuous improvement and root cause problem solving. Every one of its plants now uses that system, adapted to suit local differences in production volumes and product complexity.
Gulick sees her current role as a logical extension of the company’s existing approach to manufacturing excellence “I look at digital as the next step in our continuous improvement journey, a bit like continuous improvement on steroids,” she says. “The market has given us an amazing array of new technologies, like robots and wearable devices, and we want to use those to add more value to our continuous improvement efforts.”
First sight
The company’s first big digital success story came from the introduction of wearable devices on its production lines. The work started in 2013, says Gulick, at the time Google was developing its Glass augmented reality spectacles as a potential consumer product. Intrigued by the industrial potential of the technology, AGCO worked with technology partners to develop wearable applications for its production line personnel.
Initially, it focused on quality control and inspection activities, with a system that could guide inspectors through the complex lists of checks made to every tractor before it is released from the production line. “On our initial tests we were seeing a 32 percent process improvement though the introduction of the wearables, a result that far exceeded our expectations,” she says.
Intriguingly, much of the benefit delivered by the system came from improvements that weren’t part of the original project scope. “We were looking for a way to make our employees’ jobs easier, but the really big win came from the ability to report non-conforming products or quality issues in real time.” When inspection personnel identify and log an issue, AGCO’s system immediately alerts members of the manufacturing quality team. That allows them to take action straight away, potentially preventing a repeat of the same problem on other machines currently in production.
Those successes have encouraged AGCO to expand its use of wearable devices to other production activities. Augmented reality glasses are now being used to guide operators through complex assembly tasks, for example. “We work very closely with our people to ensure the system gives them exactly the information they need,” explains Gulick. “That means you might provide a different level of detail to staff depending on their training or experience with a given task, and you can alert them to activities that require special attention, like design changes or areas where quality issues have been identified.”
Plowing through the data
Wearable devices don’t just present data to AGCO manufacturing personnel, they generate data too, as staff click through task checklists and mark activities as complete. Together with the reams of data generated by sensors on production machines, that information is fueling another of AGCO’s digital strands: advanced analytics. The company is applying an array of analytical approaches to the data generated in its manufacturing operations, with the aim of unearthing new opportunities to trim waste, boost productivity and prevent problems.
The ability to analyze detailed production data is helping the company to improve its factory operations in many ways, says Gulick. The ability to see exactly how long each production step takes to complete, for example, helps factories to balance their lines more effectively, ensuring that people and machines don’t have to waste time between activities waiting for other operations to finish. The company is also looking at real-time analytics as a way of enabling pre-emptive action to address problems on the line. “If you know exactly how long a certain task typically takes, and the data shows that something is going unusually slowly, that might be an indicator that an employee is struggling with an issue, and maybe they need help to resolve it,” she explains.
AGCO has even built full digital simulations of manufacturing plants, allowing it to model the flow of people, parts and products through the complete production process. That’s still a costly and labor-intensive activity, says Gulick, but the approach is extremely useful in the planning of complex projects, such as building a new plant or reconfiguring production lines to accommodate several types of machine.
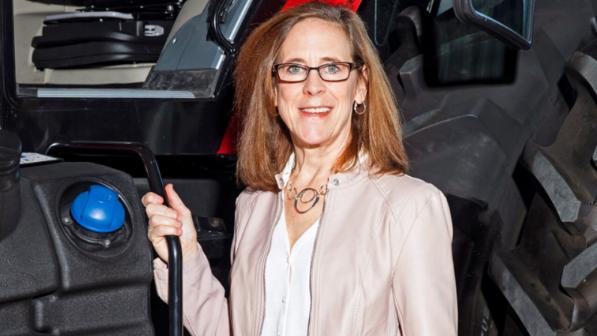
Innovative, collaborative, additive
While much of AGCO’s digital effort is designed to support its human workers, the company is also investing in advanced automation. That work has a long history. The company’s factories already make extensive use of robots in activities that play to their traditional strengths, like welding and paint spraying. And several plants use automated guided vehicles (AGVs) to move parts and machines between workstations.
Today, however, it is also making use of the latest generations of robotic systems, which offer new capabilities and additional flexibility. “Our older AGV systems follow a magnetic track in the floor of the plant,” notes Gulick. “Now we are working to bring in fully autonomous models that can navigate without those fixed guides. That’s important because it simplifies things when we want to adapt or reconfigure a facility.”
Some plants have also piloted cobots, collaborative robots designed to work safely alongside human operators. The technology is a promising one for some tasks that human workers find strenuous or tricky to complete with the required consistency, says Gulick. She notes, however, that there is still work to do before cobots are sufficiently capable, or user-friendly, for more widespread application.
One technology that has spread more quickly across AGCO’s manufacturing operations is additive manufacturing, or 3D printing. The company doesn’t yet use it for the production of components used in its finished products, but manufacturing teams are constantly coming up with new applications for the technology, from precisely shaped covers to mask parts in the paint shop to replacement components for older manufacturing machines.
Why go looking for the latest logistics stories and insights when you can have them delivered right to you?
Skills, scale and support

So how will AGCO’s manufacturing operations change most over the next five years? “A lot of people think that digital manufacturing is about replacing people with automation, but it’s really critical to understand that actually it’s about enhancing your people,” says Gulick. “There’s no doubt that the jobs our workers do are going to change significantly over the next three to five years, and that’s something we are really focused on right now. They will need to be comfortable with technology, able to work alongside automated equipment and to program these new machines. We are doing a lot of work to get our people ready for that new world, including sending staff back to school to learn about these new technologies.”
Overall, says Gulick, AGCO has plenty of reasons to push on with the development of a broad range of digital manufacturing approaches. Not every experiment pays off, she notes, but those that do often deliver value that exceeds the company’s initial expectations by a factor of three or more. Replicating its successes across the organization will help the company achieve the demanding improvement goals it has set for itself, which include a 20 percent overall productivity increase over the next five years. “Digital innovation requires you to think big, start small and fail fast,” says Gulick. “But when things do work, you need to scale even faster.” — Jonathan Ward
Published: January 2019
Images: Ackerman Gruber for Delivered.; AGCO Corporation