The pharma cold chain has become an innovation hot spot. Worldwide, the life sciences sector spends around $14 billion every year on the transport and storage of products that need to be kept refrigerated or frozen. By value, temperature-controlled logistics make up only around 20% of the total pharmaceutical logistics market, but the share of products that require special temperature treatment is rising fast.
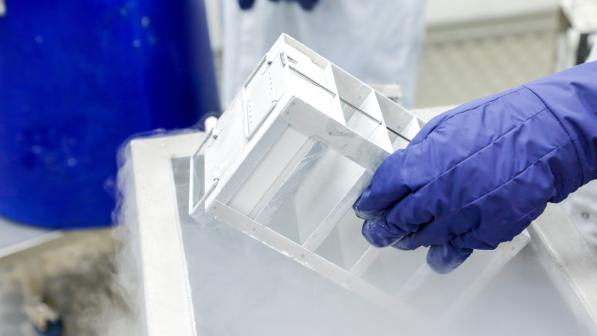
The term “cold chain” has given way to “temperature controlled” and typically refers to consistent, uninterrupted refrigeration of product through the end-to-end distribution cycle. Temperature-controlled transportation covers a broad spectrum of temperature ranges, including controlled room temperature (CRT, which refers to 15 C to 25 C/ 59 F to 77 F), refrigerated (2 C to 8 C/ 35.6 F to 46.4 F) or even cryogenic (below 0 C/ 32 F).
A wide range of drugs and related products require various forms of cold chain or refrigerated temperature-controlled storage, transportation and monitoring. They include long-established products such as insulin and vaccines, as well as newer biopharmaceutical products. By value, sales of temperature-sensitive products are rising at more than 10% annually, twice the overall growth rate of the pharma sector. And it isn’t just high-value, high-tech biological products that are driving the industry’s interest in temperature control. The Good Distribution Practice (GDP) guidelines used by many global, regional and national health organizations now require companies to understand and manage temperature-related risks for all pharmaceutical products. That is blurring the line between the traditional cold chain and conventional logistics approaches.
More worryingly, the cold chain is also a significant source of costs and quality challenges for pharma companies. The International Air Transport Association (IATA) estimates that the industry loses product worth $2.5 billion to $12.5 billion every year as a result of problems with temperature control in transit, with half those losses occurring while shipments are in the hands of airlines or airports. Add in other costs, such as the need to make and ship replacement products and to analyze and fix the root cause of temperature deviations, and the estimated total cost to the industry approaches $35 billion.
Keeping your cool
The industry has developed a wide range of solutions to control the temperature of products in transit. Pharmaceutical companies and their logistics partners can choose active cooling systems, containers that incorporate a powered refrigeration system, or passively cooled containers that incorporate a phase change material such as frozen carbon dioxide. For short journeys or “controlled room temperature” applications, they can rely on packaging or containers fitted with thermally insulating materials or blankets.
Active systems tend to offer the most precise temperature control but are expensive and bulky. Passive containers are cheaper and easier to manufacture, but they can only provide cooling for a limited period before all the phase change material is used up. Active containers require regular maintenance to ensure reliable operations, while passive units must be preconditioned before use, a time-critical process that adds complexity to logistics operations. The batteries and other materials used in either container type may be considered hazardous materials, restricting the available transport options.
For pharma players, decisions about how cold chain operations are run are complicated by factors that go beyond the choice of technology. First, there’s the need to keep supply chain costs under control. The high price of the most advanced cold chain solutions might not be a critical consideration for an advanced oncology drug that costs thousands of dollars per dose, but it is highly significant for the delivery of large quantities of vaccines to emerging markets.
Then there’s agility. Pharma players increasingly recognize the value of having multiple logistics options available to them. The ability to use different routes and transport technologies can be critical in the event of a natural disaster or supply chain disruption, for example. And agility can also help companies manage longer-term shifts in the supply chain, from demand fluctuations and the emergence of new markets to the impact of mergers or changes to manufacturing and distribution networks. In the search for solutions to these challenges, the industry is turning to the technologies of the fourth industrial revolution: big data and the internet of things.
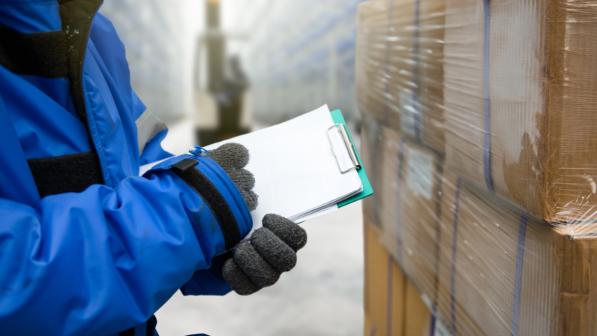
Getting smarter
At the core of the new approach to cold chain technology is the use of sensors and smart tracking devices that can be attached to shipping containers to record environmental conditions outside the box through every stage of a journey. The concept is well established: DHL, for example, has been using such external devices as standard in its Thermonet service offering across its temperature-controlled station network since 2013. What has changed is the quantity and the detail of the data available from those sensors. In part, that’s because the tracking devices themselves are becoming more sophisticated. They may contain GPS receivers that record their precise location, for example, or accelerometers to identify bumps and shocks.
Data improves the cold chain in several ways. Most simply, sensors provide an alarm function, alerting shippers when packages are being exposed to external environmental conditions that may exceed the protective abilities of the temperature-controlled packaging in use. Ultimately, this can compromise the acceptable temperature range that the product requires to ensure quality, safety and efficacy. It can also prevent the unnecessary destruction of potentially critical shipments. Many products can endure short periods of above-normal temperatures without adverse effects. An accurate record of temperatures over time allows companies to make informed judgements about whether a temperature excursion in transit was within acceptable limits.
More significantly, however, the data accumulated from thousands of shipments allows companies to build up a detailed picture of the environmental conditions experienced by products in different transport lanes, at different times of the year and with different carriers. With the benefit of modern computing power and analytical algorithms, companies can mine that data to spot trends and patterns that help them to improve supply chains. “Data analysis can reveal that, for nine months of the year, you could use passive cooling on a particular route, only requiring an active system at the height of summer or the dead of winter,” says Larry St. Onge, President, Life Sciences & Healthcare, DHL.
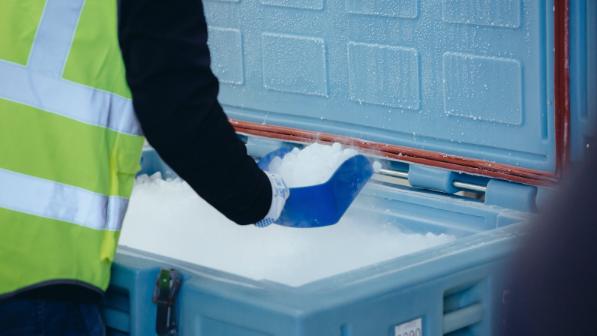
Companies can also incorporate data from other sources into their analysis. A new generation of supply chain risk management tools, such as DHL’s Resilience360 platform, can provide information on the frequency and severity of delays and disruption experienced on specific routes and key transport hubs, for example. Bringing multiple sources together allows companies to make better-informed decisions that balance cost, risk and flexibility in their cold chain planning.
Why go looking for the latest logistics trends and business insights when you can have them delivered right to you?
People still matter
Data alone can’t ensure that a pharmaceutical shipment arrives at its destination in good condition, however. Ultimately, cold chains depend on multiple participants doing the right thing, from airlines and ground handling staff to warehouse operatives. Even the best packaging will struggle to perform if it is left for hours on airport tarmac at temperatures of 40 C/ 104 F.
Ensuring adherence to good practices in product handling is made more difficult by complex rules. Supply chain participants may have to comply with a wide range of standards and guidelines, established by bodies ranging from the World Health Organization (WHO) to regional and national regulators.
The industry recognizes the importance of standardization and compliance, especially in long logistics chains with multiple stages and many different participants. Over the past five years, for example, IATA has developed and promoted a new accreditation scheme for companies involved in healthcare. The Center of Excellence for Independent Validators Pharmaceutical Handling (CEIV Pharma) certification scheme is a voluntary program that aims to “improve the level of competency, operational and technical preparedness” of organizations across the supply chain.
By mid-2018, IATA says 220 locations worldwide had received CEIV Pharma certification, with another 75 in the process of certification. DHL is undertaking a global rollout of the approach across all the locations it uses for pharmaceutical logistics. At the time of writing, more than 30 DHL facilities have been certified under the scheme.
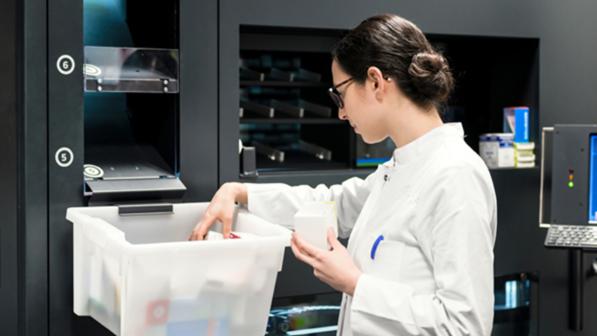
New challenges ahead
Even as the industry applies new technologies and smarter management approaches to its existing cold chain processes, further complexity is on its way. Innovations at the front line of medical science are putting the patient at the center of the healthcare supply chain. Autologous cell therapies will require sophisticated two-way cold chains that can take samples from patients to manufacturing facilities, where they are used in the production of fully personalized treatments. The growth of e-commerce and at-home delivery of therapies may add complexity in last-mile deliveries of sensitive products. And across the developing world cold chains will need to scale up significantly to meet rising demand. One quarter of the world’s diabetic population lives in China, for example, but the country currently receives only 6% of global insulin production. The race to build more efficient, intelligent and reliable cold chain logistics operations is set to heat up as the life sciences sector prepares for the healthcare challenges of tomorrow. — Jonathan Ward
Published: June 2019
Images: iStock