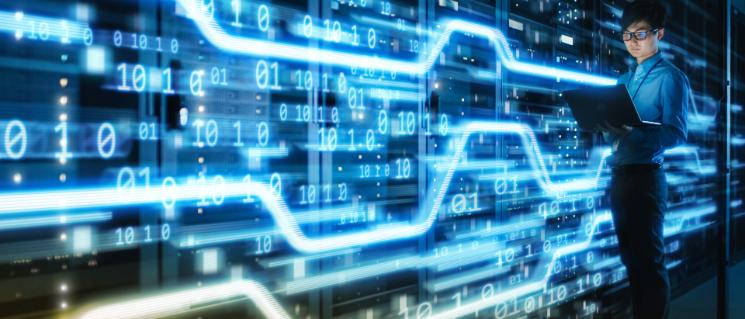
Innovation
Bring on the bots! How automation can break through bottlenecks
DHL Global Forwarding, Freight has integrated robotic process automation to automate (and even eliminate) time-consuming tasks and free up people for more value-adding tasks and improved customer service.
The end of the tedious task?
To move goods around the world – whether by land, air, or sea – you need a lot of people. It’s a multifaceted business that involves brokering between customers and carriers, handling complex customs processes, managing multimodal transportation solutions, and more. That’s why DHL Global Forwarding, Freight (DGFF), the world’s leading provider of air, ocean, and overland freight-forwarding services, employs over 40,000 people. To help deliver the most efficient routing and transport services possible, 4,500 of them work at the company’s five Global Service Centers (GSC). These shared services hubs support DGFF’s global logistics operations and provide back-office functions like finance.
Despite the increase in digital technology, the forwarding and freight business remains dominated by manual processes. The question was whether DGFF could change that.
Enter robotic process automation (RPA). This technology allows users to configure computer software – in other words: a bot – to imitate how a human executes a process within a digital system. Could we leverage the latest RPA technology to reduce the need for human intervention in certain processes? If yes, DGFF could remove bottlenecks and free up internal resources for more value-adding tasks by automating and even eliminating time-consuming, repetitive tasks.
Ultimately the goal was to expand and optimize shared service capabilities and empower employees to better meet customers’ needs.
50 %
DGFF’S RPA PILOT PROJECT SAW AN IMMEDIATE 50% INCREASE IN EFFICIENCY.
500
RPA ROBOTS NOW HANDLE THE WORKLOAD OF 500 FTES, FREEING PEOPLE UP FOR MORE REWARDING, VALUE-ADDING WORK.
160
DGFF HAS DEPLOYED MORE THAN 160 UIPATH-BASED BOTS SO FAR.
"Post Flight" pilot delivers unexpected ROI
DGFF partnered with UiPath, the world’s leading RPA software company, to create a global process automation hub. The plan was to use innovative technologies, such as RPA, to streamline vital internal processes and boost the performance of DGFF’s shared-services model.
The project began with a thorough examination of just about every part of the GSC model to identify those processes that required manual intervention. Initial efforts focused on uncovering processes that relied on tedious sub-tasks for a high volume of transactions using business rules or structures. These would be the best candidates for automation and possibly deliver some “quick wins.”
To test the potential of robotic process automation, a pilot project dubbed “Post Flight” was started. A robot extracted data from the DGFF’s operations system and combined it with critical flight data, such as whether or not a partner’s flight was on time. The Post Flight bot then produced a report that identified potential problems. This allowed the operations team to focus their attention and avoid wasting time checking things that were running smoothly.
The automated insights proved extremely valuable, but it was the immediate internal efficiency gains that caught everyone’s attention. Before the bot was deployed, a team of 30 was needed to complete the process. With the RPA platform in place, only 15 of them were now needed. This leaner team now manages the task based on the automatically identified exceptions, which increases supply chain transparency and improves the service to the customer. What’s more, the other 15 people were freed up to take on higher-value, more rewarding roles.
All of these results added up where it mattered most: higher service quality at significant cost savings and with an impressive return on investment.
What is Robotic process automation?
Robotic process automation (RPA) is a form of business process automation technology based on software robots (bots) or artificial intelligence (AI). It is sometimes referred to as software robotics, but should not be confused with robot software. The technology allows users to configure computer software or a bot to imitate how a human executes a business process within a digital system. Just like humans, these bots capture data and manipulate applications via the user interface. They are able to perform a wide variety of repetitive tasks, such as logging into applications, connecting to system IPAs, moving files and folders, extracting data, and more. The difference is that they are faster and much more efficient than humans. Bots don’t make mistakes and can work 24/7.
RPA works differently than traditional IT solutions in that it less intrusive and leverages existing infrastructure without disrupting the underlying systems. This speeds up the development process and reduces costs.
Process automation becomes a valuable shared service
After the pilot exceeded expectations, the full potential of RPA technology was clear. The project team quickly set out to achieve the original vision: providing process automation as a new service for the entire DGFF organization.
To do this, the company created a Center of Excellence (CoE) and a Virtual Delivery Center (VDC). The CoE was set up to define standards for robotic process automation at DGFF to help business partners and employees understand how it works and the added value it offers. The center helps all stakeholders explore and promote opportunities based on RPA technology as well as share lessons learned and best practices.
The Virtual Delivery Center is a new unit within the Global Service Center. With a team of nearly 30 people, the VDC provides process automation as a service within DGFF. Their mission is to closely examine a specific process, employ RPA technology to automate it, and then take that new bot and share it with other DGFF service centers and facilities around the world. This means services that were once provided manually can now be automated and provided virtually – a perfect example of man and machine working hand-in-hand.
Want it Delivered?
Why go looking for the latest logistics trends and business insights when you can have them delivered right to you?
What’s next?
DGFF now sees a future where the shared service center and the organization as a whole can integrate robotic process automation into other advanced technologies, such as smart optical character recognition (OCR), machine learning and artificial intelligence (AI), to further automate how structured and unstructured data is captured and analyzed. Now that the right model and platform is in place, it is possible to envision one holistic service management platform to orchestrate an efficient team of humans and bots that provides ever improving service to customers.
Published: October 2020