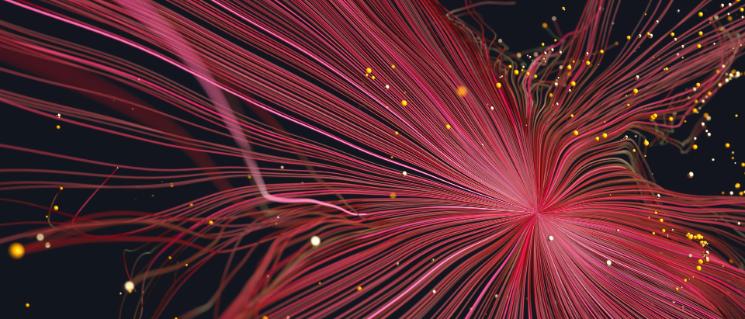
Tech-Tonic Shift: How the sector responded to the pandemic boom
In a tumultuous year, the technology sector has boomed. But stronger than expected growth has brought its own supply chain challenges.
The humble laptop computer is the unsung hero of the technology world: widely used, but rarely loved. Journalists and industry analysts have been forecasting the demise of the category for years. Supported by the internet and cloud computing technologies, smart phones and tablets can already do most things people once needed a “proper” computer to accomplish, and those devices don’t need to be lugged around in a heavy, dedicated bag.
Then the world changed. In 2020, after years of stagnant growth, PC sales spiked by more than 10% to around 300 million units. You don’t need to be a market research specialist to see why. The COVID-19 pandemic forced work, study and social lives to change overnight. Instead of catching up on emails in the airport business lounge, jet-setting executives were confined to their home offices or spare rooms for months. Teachers taught classes via video conference. Even family gatherings shrank to a grid of faces on a screen. In this strange new environment, the unglamorous laptop suddenly looked like the best tool for a multitude of jobs.
It wasn’t just end user devices that experienced an unexpected boom during 2020. Behind the scenes, a wide range of technology-based companies also saw a surge in demand. Providers of video conferencing services had to cope with thousands of new users. E-commerce activity spiked as health protection measures kept shoppers out of stores. Many of the organizations that provide these services needed to buy or rent significantly more server capacity to keep their systems running.
Meeting the need
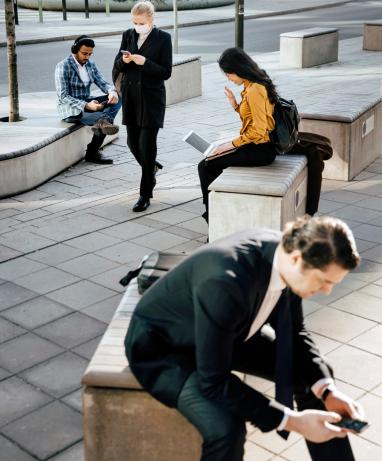
In a period when the global economy was enduring its deepest recession since World War II, forecast-beating sales figures put the technology sector in an enviable position. Yet fulfilling last year’s surging demand created significant challenges across the industry.
The sales spike wasn’t the main problem. In a business driven by rapid innovation and short product lifecycles, technology players had become extremely adept at ramping production and distribution up or down as needed. But until now, they haven’t had to perform these supply chain gymnastics in the middle of a pandemic.
For equipment makers, the initial worry was manufacturing capacity. The countries hit first by the pandemic were the same countries that play a central role in much of the technology supply chain, from the production of semiconductors to the assembly of finished products. The strict lockdown in China’s Hubei province sparked fears that government-imposed restrictions would paralyze economies across the region, with factories forced to close.
Ultimately, however, it was wider supply chains that proved the more significant challenge. The effective response by health authorities across Asia allowed countries to keep their economies moving, but the growing crisis disrupted economic activity right around the world, forcing companies to rethink their global logistics and distribution networks.
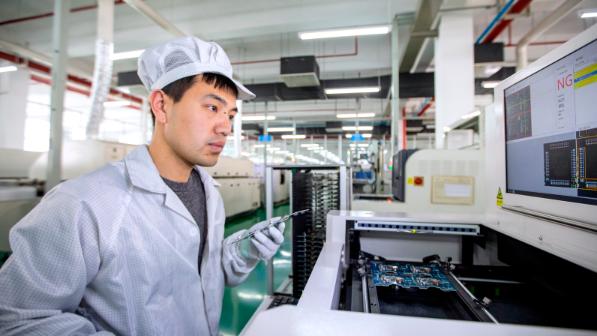
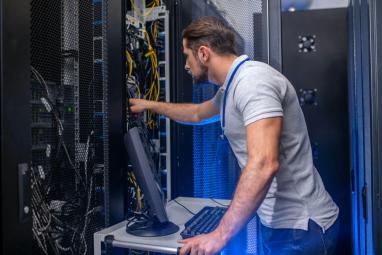
Every industry faced logistics complexities during the pandemic as countries introduced tighter border restrictions, delaying the movement of critical shipments. In the technology sector, however, it was the dramatic reduction in airfreight capacity that created the biggest problems. High-tech companies have long relied on airfreight to distribute their small, high-value products, and much of that freight travels as belly cargo in scheduled passenger jets. When the crisis brought international passenger travel to a standstill, that capacity disappeared from the skies.
“There was obviously a lot of work required to replace belly cargo capacity,” says Alexander Gunde, President, Global Technology Sector, DHL. “But we also saw our technology clients changing their logistics models to accelerate the flow of products to their customers.”
For a number of customers, he continues, this involved bypassing regional distribution centers altogether and shipping products directly to end users. “They had supply chains that were set up for B2B logistics, with large shipments to a small number of destinations. Suddenly, they needed to operate in a B2C mode, moving individual products to thousands of customers around the world.”
The next phase
A year into the pandemic, the situation is beginning to stabilize. Technology companies are meeting customer demand for most products, although supply in some component categories remains tight as companies ramp up production or build inventories in anticipation of a broader economic recovery. But the crisis may have a long-term impact on the design and operation of supply chains.
“The most obvious change among many of our customers is an increased focus on risk and resilience,” says Gunde. “Traditionally, technology companies have tried to balance cost and speed in their supply chains. Now they are also asking how those supply chains will perform in the face of disruptive events.”
COVID-19 certainly brought the importance of resilience to the front of the mind, but the issue has been climbing the agenda for some time. Researchers at the McKinsey Global Institute estimate that companies experience a supply chain disruption lasting a month or more once every 3.7 years. And that’s a cross-industry average.
The tools available to improve supply chain resilience are also quite well known, if not yet universally applied, says Gunde. “Good visibility and transparency in the supply chain are critical when you need to make quick decisions in the face of disruption. Over the past year, companies that were more advanced in digitalizing their operations and their supply chains were better able to respond to the challenges of the pandemic. Now everyone wants to be in that position, so we expect the crisis to further accelerate the digital trend.”
The desire for better information flows is also encouraging technology players to expand the scope of their supply chain risk management activities. “Companies realize that knowing the situation in your distribution network and at your first-tier suppliers is not enough,” says Gunde. “You also need visibility on the state of the supply chain in the second and third tiers, and beyond.”
Then there’s the question of geography. Before the coronavirus, rising trade tensions were already encouraging U.S. companies to reduce their reliance on China for critical components and manufacturing services. Now technology companies all over the world are re-evaluating the risks and benefits of having large parts of their supply chains concentrated in just a few locations.
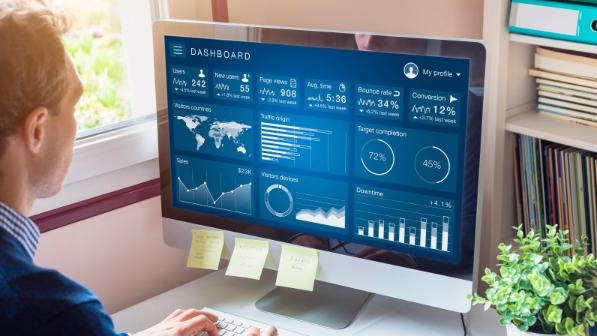
“There has been a lot of discussion about reshoring production from Asia to the U.S. or Europe,” says Gunde. “And we do expect a certain amount of supply chain reconfiguration, especially in the final assembly of products. Assembling closer to the end user makes a lot of sense with complex or highly customized products, allowing companies to respond quickly to shifts in demand.”
10
Percentage by which PC sales spiked in 2020, after a decade of decline, increasing to around 300 million units
3.5
Percentage of reduction in global GDP during 2020 as a result of COVID-19
Nevertheless, today’s supply chain setups have some compelling advantages, including established networks of suppliers and access to technical expertise. “Technology companies want to manage risks while retaining those benefits,” says Gunde. “One way they are doing that is by expanding production to other countries within Southeast Asia. In recent months, we have seen a significant rise in shipments from Vietnam to Europe and North America, for example.”
Want it Delivered?
Why go looking for the latest logistics trends and business insights when you can have them delivered right to you?
Climate change – a hot topic
Some risks can’t be mitigated by smart supply chain reconfiguration. The COVID-19 pandemic is estimated to have caused a 3.5% reduction in global GDP during 2020.
As the world plots its path out of the current crisis, there is broad consensus that action on climate change is now urgent. Governments, investors and consumers are all putting pressure on companies to create clear plans to reduce or eliminate greenhouse gas emissions by the middle of the century.
“Previously, we considered digitalization, resilience and sustainability as separate topics,” says Gunde. “We see now that they are interconnected. Supply chain visibility helps companies to become more resilient and cost effective in the long run. And supply chain optimization helps to reduce carbon emissions through more efficient planning of loads, routes and transport modes.”
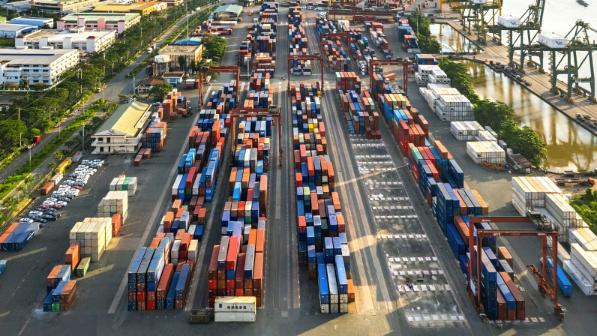
In the coming years, the drive for more sustainable technology supply chains is likely to spur innovation on multiple fronts. “In transportation, you can become more sustainable in two ways,” says Gunde. “You can burn less fuel by minimizing travel distances or switching from air to rail or sea. And you can burn cleaner by using electric vehicles for the short routes and alternative fuels for longer routes. Over the long term, a combination of both approaches will be required.” — Jonathan Ward
Published: June 2021
Images: Benis Arapovic/ddp; Adobe Stock; Deepol/plainpicture; Dmytro Zinkevych/mauritius images; Zhai Huiyong/dpa; Shutterstock