Normally, Wickert transports the WKP 10,000 S to customers by boat – they are too large for being transported by airplane.
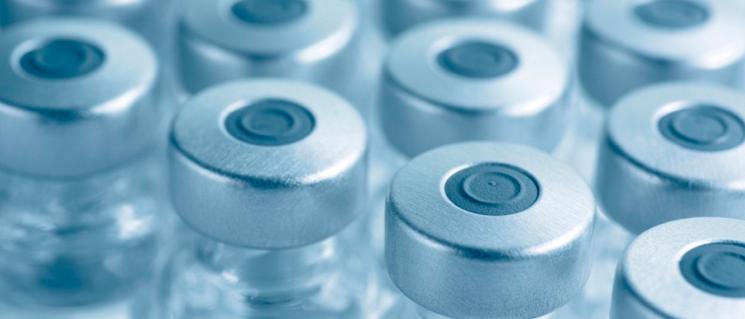
Global Trade
The stoppers that make the vaccine go
From syringes to medical personnel administrating each dose, there are many essential pieces to the puzzle when it comes to distributing coronavirus vaccines around the world. But here’s one you may not have considered: tiny rubber stoppers that seal vaccines doses in vials – and the unprecedented transport and manufacturing effort that enabled their production at a giant scale.
Rubber stoppers, pressing needs
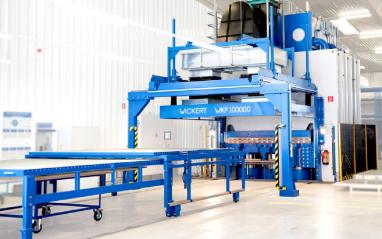
What do a 45-ton hydraulic press, one of the world’s largest airplanes, and a tiny rubber stopper have in common? They’ve all been mobilized as part of the global fight against the coronavirus pandemic.
The story begins in southern Germany, home of a company called Wickert. The family business is known for its clean-room and pharmaceutical presses. One of their products – the WKP 10,000 S, to be exact – is used to manufacture rubber stoppers, which are needed to seal high-purity vaccine vials containing doses of the coronavirus vaccine.
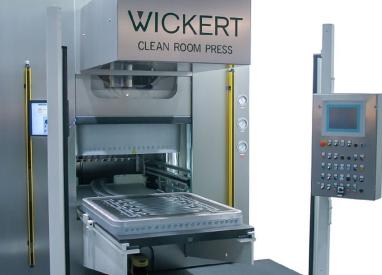
As soon as it was clear that vaccine manufacturers would be in urgent need of billions of rubber stoppers, Wickert sprang into action. Normally, it takes 10 months to deliver the massive and complex WKP 10,000 S to customers. Responding to the urgency of the pandemic, the team at Wickert was able to cut the delivery time down to six months.
By the time the international pharmaceutical industry was ready to begin churning out vaccines, the machines were ready to go. But there was just one problem: the machines were in Germany, and some of the vaccines were being manufactured in the US. Cue the DHL rubber stopper mission.
Big, bigger, Antonov
Normally, Wickert transports the WKP 10,000 S to customers by boat – they are too large to make transport by airplane a feasible option in most cases. But with the clock ticking on vaccine production, every day counted. That’s when DHL stepped in: With no way to reduce the size of the machines, we just found a bigger plane.
The AN-124-100 airplane operated by Antonov Airlines is one of the largest birds in the sky. With a cargo capacity of 150 tons, it is the only plane robust enough for the job of transporting the WKP 10,000 S machines to the US (a payload of 100 tons per delivery).
Utilizing both ends of the AN-124-100’s cargo loading bay, external cranes, and the plane’s onboard loading systems, DHL worked with Wickert and Antonov Airlines to make sure the eight transport flights from Frankfurt, Germany to two destinations in the United States went as smoothly as possible. Even when a snowstorm forced one of the flights to land at a different airport, all deliveries were still completed as scheduled.
A real big mouth
An error occurred while loading the video.
Timelapse video of the AN-124-100's cargo loading at the Frankfurt-Hahn (HHN) airport.
By opting for the more complex delivery option using DHL and the Antonov Airlines plane, Wickert shaved 25 days off the delivery time to its pharmaceutical customers. That meant the WKP 10,000 S machines were up and running as quickly as possible – producing 2,000 of the essential rubber stoppers per stroke of the press.
The tiny rubber miracles must be manufactured to government-mandated specifications and must function flawlessly at extremely low temperatures – much like the vaccines themselves.
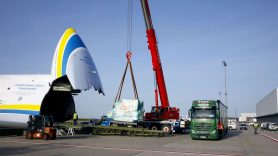
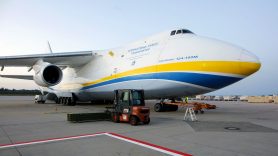
But with the clock ticking on vaccine production, every day counted. That’s when DHL stepped in.
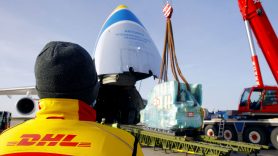
The AN-124-100 airplane operated by Antonov Airlines is one of the largest birds in the sky.
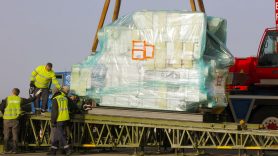
With a cargo capacity of 150 tons, it is the only plane robust enough for the job of transporting the WKP 10,000 S machines.
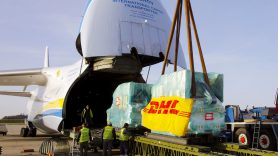
Utilizing the Antonov's cargo loading bay and external cranes, DHL made sure the transport flights went as smoothly as possible.
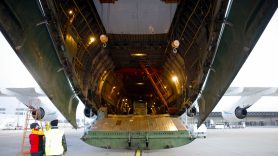
By opting for the more complex delivery option using the AN-124-100 plane, Wickert shaved 25 days off the delivery time.
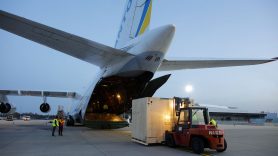
The WKP 10,000 S machines were up and running as quickly as possible – the rubber stopper mission was a success.
Creating success: the rubber stopper mission
Want it Delivered?
Why go looking for the latest logistics trends and business insights when you can have them delivered right to you?
10 billion doses
Our rubber stopper mission to coordinate this essential link in the vaccine distribution chain is just one of many transport-related roles DHL has taken on in the fight against COVID-19. From personal protective equipment (PPEs) and mask deliveries to shipping actual vaccine doses, it has been clear to us from the beginning of the pandemic that getting the logistics absolutely perfect would be one of the keys to putting the worst of it behind us.
That’s meant a number of innovations, such as optimizing supply chain operations for pandemic resiliency or expanding cold-transport solutions for sensitive doses of certain vaccines.
Transporting Wickert’s hydraulic presses involved one of the mightiest planes ever built, but it was worth the effort to ensure the humble rubber stoppers found their way into billions of vials containing our best hope to overcome the pandemic.
Published: May 2021