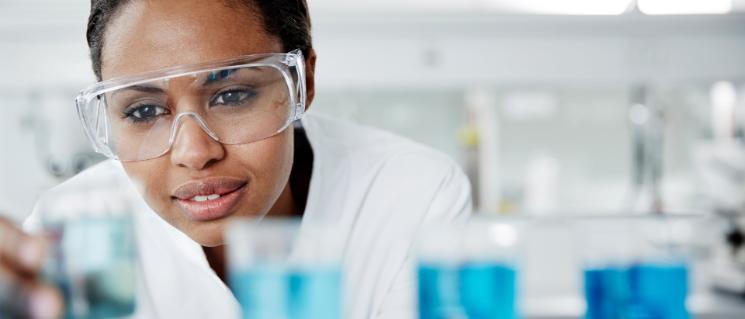
Innovation
Ingenious supply chain solutions for revolutionary vaccines
Pfizer’s revolutionary COVID-19 vaccine needed an equally ground-breaking approach to logistics.
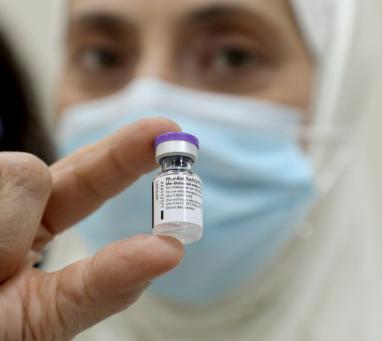
The development of effective vaccines has been the great scientific and industrial success story of the coronavirus pandemic. Intense collaborative effort between researchers, pharmaceutical companies and clinical teams slashed the time required to formulate, test and scale up production of the new vaccines from years to just a few months.
Yet delivering those vaccines at speed to millions of people around the world is an extraordinary challenge. And for U.S.-based Pfizer, that challenge was compounded by the need to transport and store everything at ultra-cold (-75ºC) temperatures, to protect the delicate mRNA molecules at the heart of its product.
The task of devising and rolling out a suitable logistics system for the vaccine fell to the company’s supply chain team, led by Tanya Alcorn, Vice President, BioPharma Global Supply Chain. “The fact that our vaccine required a deep-frozen supply chain was novel,” she says. “So right from the start, we were getting a lot of questions. How could we build the necessary infrastructure? Would there be a lot of wasted doses? Were we trying to achieve the impossible?”
The widespread skepticism became “… a catalyst and a motivator,” says Alcorn. “We said: you know what, if anyone can do this, Pfizer can. We have the best manufacturing and supply chain leaders in the industry. We have the best temperature logistics engineers, and we knew we could rise to the challenge.”
On target
And that’s what they did. Between December 2020 and May 2021, Pfizer distributed more than 15,000 shipper boxes containing 440 million vaccine doses to almost 15,000 destinations in 92 countries. Of those shipments, 95.7% arrived within three days, and an astonishing 99.996% of them met the company’s stringent temperature and quality control requirements, which were tested at multiple checkpoints in the transport process.
440 million
Number of vaccine doses Pfizer shipped to almost 15,000 destinations in 92 countries between December 2020 and May 2021
95.7
Percentage of vaccine shipments that arrived within three days at their destination
Achieving that level of performance required the Pfizer team to build its supply chain from a clean sheet, paying close attention to every step in the process, and to the way the many moving parts of the system worked together. At its manufacturing plants, Pfizer removed the racking from finished goods warehouses and transformed them into “freezer farms” containing hundreds of ultra-cold freezers to safely store vaccines as they came off the production line. It installed equipment for the on-site production of dry ice to keep the product cold in transit.
About a box
And it designed a new type of box. Tertiary packaging doesn’t usual take center stage in a major supply chain engineering project, but Alcorn explains that the bespoke shipper, used for transporting products all the way from Pfizer’s plants to end users at vaccination centers, has played a fundamental role in the design and successful execution of the entire supply chain – ultimately allowing Pfizer to achieve its vision of “breakthroughs that change (patients’) lives.”
“When we started thinking about the supply chain, we had several guiding principles for the shipper,” she says. “First, it had to be easy and efficient to use. We were going to be performing this on a massive scale, so everything needed to be easy to ‘pick and pack,’ and light enough for a person to handle without risk of injury.
“Second, we needed the shipper to be able to maintain the temperature required for our product, and not just for the typical two to four days,” she says. “Our goal was up to 10 days.” The extra time had multiple potential benefits, she explains. It would reduce the pressure on Pfizer personnel and their logistics partners, so the supply chain wasn’t “rushed.” It would ensure vaccines could be delivered safely to remote locations requiring complex multi-leg journeys. And on arrival, it would enable the shipper to be used as temporary storage in places where no conventional freezer was available – which was an important element in Pfizer’s mission to ensure equity and equal access of their vaccine to all countries, regardless of infrastructure.
In addition, says Alcorn, they wanted the shipper to be reusable, with empty units returned to Pfizer to be later refilled with fresh vaccines. That would reduce the environmental footprint of the program.
It quickly became clear that no off-the-shelf product could meet Pfizer’s requirements, so the supply chain team developed their own tailored solution. The final product uses a combination of efficient thermal insulation and dry ice to keep the vaccines cold, while a flexible internal design allows a single box to hold between one and five trays, each tray containing 195 vials of vaccine, enough for more than 1,100 doses. That flexibility was essential, says Alcorn, allowing shipments to be tailored to the needs of different vaccine programs around the world. At maximum capacity, the shipper can hold almost 6,000 doses, ideal for large mass-vaccination centers and countries that operate their own centralized storage and last-mile distribution systems. A single tray is suitable for direct shipment to smaller local centers.
In use, Pfizer’s custom shipper has met all its design goals, says Alcorn. Unopened, the boxes keep vaccines at ultra-cold temperatures for the target 10 days. On the very longest and most complex routes, shippers can be “recharged” with fresh dry ice to extend that period even further. And thousands of vaccination sites around the world are using the shippers as temporary freezers, holding the product safely for up to 30 days.

Real-time results
Pfizer’s custom shipper includes another innovative marvel: Embedded into every box is a tracking device that continually monitors temperature and GPS location and detects tampering. Data from the trackers is transmitted wirelessly though mobile phone networks to a three-tiered system of 24/7 control towers, giving Pfizer and its logistics partners real-time, end-to-end visibility of the entire supply chain. “This was a real first for us at Pfizer,” says Alcorn. “We had run some small-scale pilots of real-time tracking in the past, but this is the first time we’ve used this technology at scale.”
For the vaccine supply chain, the real-time tracking system has a simple goal: To ensure end users receive the quality vaccines they need, at the time they need them. To achieve that objective, the system is tightly integrated with Pfizer’s other supply chain management systems, all the way back to its manufacturing plants.
“At any one time, we have around 3,000 shippers in transit,” says Alcorn. “In collaboration with our technology provider and our logistics partners, we have developed playbooks that determine the actions we take in response to an alarm from any one of them.” After an initial triage process at the first-tier control tower run by the technology provider, information from an alarm is forwarded either to relevant logistics provider’s control tower, or to Pfizer’s in-house control tower.
99.996
Percentage of vaccine shipments that met the company’s stringent temperature and quality control requirements
3000
Number of shippers with vaccine doses in transit at any given time
“In many cases, the logistics partner is able to take immediate action to investigate and rectify an issue,” says Alcorn, adding that DHL’s own control tower set-up provided significant inspiration for Pfizer’s version. “If a problem can’t be fixed, as would be the case if there was a significant temperature deviation, real-time notification often allows Pfizer to take mitigating action before the issue affects the customer.” Typically, she says, the problem shipment will be stopped in transit, then a replacement order is immediately dispatched from the appropriate Pfizer site.
Want it Delivered?
Why go looking for the latest logistics trends and business insights when you can have them delivered right to you?
What’s next?
When Alcorn spoke to Delivered. in July 2021, many countries were still midway through their vaccination campaigns. Plenty were still in the early stages. The Pfizer supply chain team was busy expanding its program to new markets around the world, but it must always keep one eye on potential future developments.
“Some regions are now changing their strategy, with a shift away from mass vaccination centers to smaller local healthcare facilities,” she says. To serve those locations, Alcorn’s team has developed a smaller pack size, holding up to three sets of 25 vials. Pfizer is also working on a pre-diluted “ready-to-use” version of its vaccine, which will be easier for healthcare staff to prepare, and will potentially last for up to 10 weeks in a standard medical refrigerator. Scenario planning is underway for potential booster campaigns, and the company has announced that it is conducting a trial of a modified version of its vaccine targeting recent variants of the SARS-CoV-2 virus.
Alcorn, who after the interview was about to take her first week off work for many months, is looking forward to the opportunity to recharge by spending some time with her family. “When we began this project, we expected to reach 600 million people during 2021, we are now on track to reach 1.3 billion by the end of the year,” she says. “We couldn’t have done that without being bold in our ambition, and our success is down to the talent and effort of our teams right across the organization.
“Nor could we have done it alone. We have benefitted from some great partnerships – with customers, with regulators, and with our logistics providers.” — Jonathan Ward
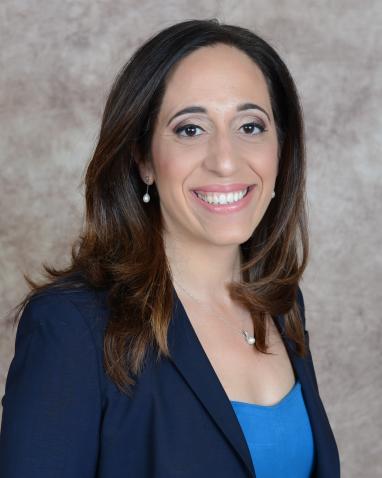
Tanya Alcorn
Vice President, BioPharma Global Supply Chain, Pfizer
With a background in microbiology, Alcorn began her Pfizer career working at one of the company’s biologics plants. After a decade in manufacturing operations, she moved into the supply chain role eight years ago, via a stint in the company’s corporate strategy function. The transition was a natural one. She notes, “I always say that when you work at a plant, everyone is a supply chain person. Your ultimate goal is to deliver the best quality product out the door so it can make a positive change in people’s lives.”
Published: August 2021
Images: Joern Wolter; Pfizer; Adobe Stock