It’s like magic. Layer upon layer of heated plastic or metal is injected from the nozzle of a 3D printer onto a plate, where it builds up into a three-dimensional object. It makes for a wondrous sight to see a tool or a toy, a prosthetic limb or a spare part for a jet engine being produced before your eyes.
It’s a process that has the potential to transform both industrial production and the supply chain. Products can be made at a fraction of the cost of manufacturing processes such as forging, molding and sculpting, as there is no need to build special equipment to create each new product.
Already, 3D printing, or additive manufacturing, has moved beyond the experimental stage, and is being used in a variety of applications where often the parts are complex to produce or require high levels of customization.
Game-changer
DHL has investigated the future of 3D printing in an in-depth study that looks at the implications and uses of the technology across sectors and the supply chain.
The report – “3D Printing and the Future of Supply Chains” – concludes the technology will “undoubtedly be a game-changer in many industry segments” and will lead to improved product quality and, in some cases, completely new types of products. It highlights a number of use cases where 3D printing could have a disruptive effect and implications for the future of supply chains. Companies could team up with logistics providers offering 3D printing in areas such as “spare parts on demand,” which would enable them to save substantial amounts on storage; end-of-runway services, to enable fast production of parts that need to be put into operation in the shortest possible timeframe, or product postponement services to increase customization options but at the same time reduce lead time to the customer.
The promise for 3D printing comes as new industrial applications of the technology are springing up all the time. The report says Airbus has already introduced 1,000 3D-printed parts to its A350 airliner model. Each part weighs just half as much as the one it replaces, significantly reducing the weight of the aircraft.
Airbus has heralded a breakthrough by producing a partition wall for its planes through 3D printing. This product is billed as the world’s largest 3D-printed airplane cabin component. The partition wall, which fits between the passenger seating area and the plane’s galley, has a bionic structure, mimicking the structure of organic cells and bones. The new design dispenses with the weight, materials and bulk of older versions of the partition and is 45 percent lighter than previous versions. It is also much stronger, supporting the jump seats used by cabin crews. When installed in the fleet of A320 planes, Airbus claims it will save up to 465,000 metric tons of CO2 emissions each year.
Rocket Parts
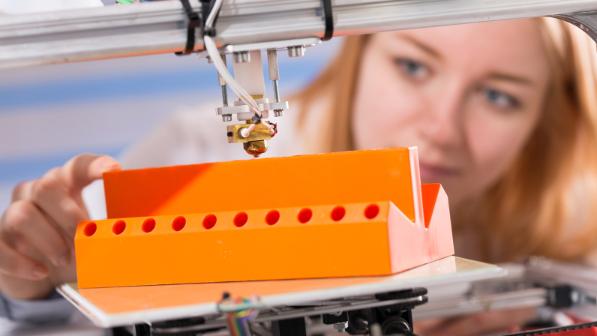
Meanwhile, U.S. space program NASA is experimenting with ways of printing rocket parts, and has manufactured and tested 75 percent of the parts needed to build a 3D printed rocket engine. The turbo pumps, injectors and valves have been successfully tested together, suggesting it would be possible to build a 3D engine for landers, in-space propulsion, or the upper stages of the rocket engine. NASA has also manufactured 3D-printed objects on the International Space Station (see box).
General Electric (GE) has also made some big commitments to 3D printing. The industrial giant recently opened The Center For Additive Technology Advancement (CATA), producing 3D-printed parts such as fuel nozzles for jet engines. GE is investing $40 million in the facility, which will develop industrial applications for 3D printing across its businesses.
BMW Group has integrated 10,000 3D-printed parts into production of the Rolls-Royce Phantom. The complex geometry of some of the parts required lent itself to 3D printing, and they could be manufactured significantly faster than with traditional methods without any loss of quality. BMW is now planning to roll out 3D printing technology across its production range.
Meanwhile, Dubai’s Museum of the Future project has unveiled what it calls the world’s first 3D printed office building. A 3D printer was used to create the building layer by layer, using cement. It took 17 days to print the 250 square meter building at a cost of some $140,000. The printer used to make the building – including all interior furnishings and detailing – is 120 feet (36 meters) long, 40 feet (12 meters) wide and 20 feet (6 meters) high.
3D printing also has huge potential to help developing nations provide basic supplies to people living in remote areas. According to the DHL report, startup re:3D is donating a “Gigabot” to some of these communities to make clothing and other products on a day-to-day basis. Another firm, Field Ready, is collaborating with World Vision to establish an innovation lab in Nepal to produce 3D-printed supplies for relief camps – reducing aid agencies’ logistics costs by 40-50 percent.
Why go looking for the latest logistics trends and business insights when you can have them delivered right to you?
Sales growth
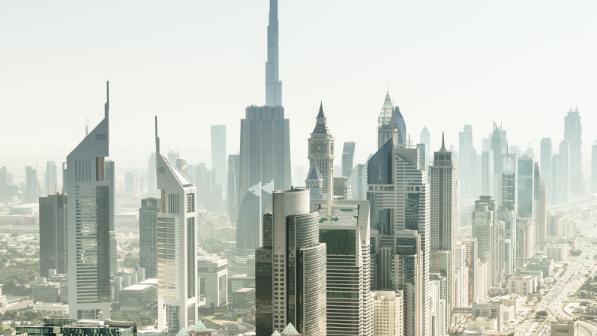
Sales of consumer-grade printers priced at under $5,000 from companies such as Ultimaker and Makerbot have grown rapidly. In 2015, some 258,000 were sold globally, up from 35,500 in 2012.
“Affordable desktop printers are expanding tremendously in sales and adoption, moving into places in industry and engineering in a bigger way than before,” says Matt Griffin, Director of Community, North America, for 3D printer manufacturer Ultimaker.
He explains that, in the same way low-cost PCs are networked together, a similar process can be used with consumer-grade 3D printers to set up a small production line that makes all the components for a particular product.
“Each machine is like a unit of production, it will do whatever it is assigned with the materials available to it,” says Griffin. “You can deal with these magic [production] numbers between 100 and 1,000 products, where there isn’t enough of them to make it worth setting up tooling for injection-molding or any other processes.
“That is actually very interesting when you can leverage this kind of system to produce something really quickly. You can respond to a need or a trend quickly, and get the entire object produced without necessarily needing to make a business case to produce 10,000.”
In the short term, industrial-grade 3D printing – where printers can cost upwards of $1 million – is likely to complement existing production and delivery techniques rather than directly replacing them. The challenge in the longer term is to improve the technology and make the printers faster and more agile, able to use multiple materials and capable of producing higher-quality items.
As these challenges are met, 3D printing is likely to lead to greater customization of goods and
localized production. There is no doubt that additive technology will develop and enhance manufacturing and logistics in the years to come. But just like the technology itself, the changes will unfold step by step. — David Benady
Published: November 2016
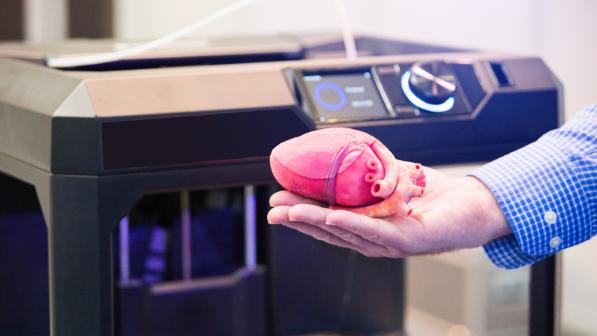
Life Sciences & Healthcare
Great strides are being made with 3D printing in life sciences and healthcare. At the University of Melbourne, engineers and doctors have worked together to model and 3D print the heart arteries of patients. The models allow doctors to see the twists and blood flow in these vessels and accurately construct the most suitable heart stent, a mesh tube used to support narrow or weak arteries.
In collaboration with researchers at the University of Wollongong’s ARC Centre of Excellence in Electromaterials Science, the team is able to print a patient’s artery within a day.
Their aim is to improve the technology so they can print the artery while the patient is in surgery – and ultimately, to be able to 3D print a custom heart stent on the spot.
“No two arteries are shaped the same,” says Professor Peter Barlis, Honorary Principal Fellow at Melbourne Medical School and Melbourne School of Engineering.
“We’ve gone to our engineers and created 3D models looking at a million data points in the artery. We want to use models to predict the best type of stent for a patient. Once this process is streamlined, we can have a patient on the table and an artery 3D-printed and modeled to guide the procedure.”
Other medical teams have used 3D-printed heart models to prepare for complex surgical procedures – especially when operating on babies and young children.
Aerospace
Airbus has unveiled a drone made of parts that have been 3D printed in polyamide. The initial version of the THOR (Testing High-tech Objectives in Reality) aircraft weighs 21 kilograms, can fit in a four-meter by four-meter square and is powered by two 1.5-kilowatt electrically-driven propellers. Airbus says the time taken to produce the prototype was much shorter than with traditional methods – seven weeks to print the THOR aircraft’s 60 structural segments, with one week for assembly and three days for finetuning. “The first version was to test whether the slogan ‘Print me an airplane’ can be converted into reality,” says Detlev Konigorski of Airbus’ Emerging Technologies & Concepts activity in Germany, who oversees the THOR project. “The first flight was simply about flying. Now, we want to generate basic data on things like altitude, speed and acceleration in a turn.” Follow-on THOR versions are being assembled at the new Center of Applied Aeronautical Research in Hamburg. The second THOR version will have interchangeable wings, including concepts for a hexagonal wing with a support structure derived from a honeycomb design; a metallic aluminum wing; and a flexible wing made from carbon-fiber-reinforced plastics.
“If a THOR aircraft takes off, and after 30 feet (9 meters) makes a nose-dive back to the ground, our attitude is, ‘Good, let’s sweep it off the runway and come up with a better idea’,” says Konigorski. “In a few weeks, we can print a new aircraft!”
Space engineering
The International Space Station’s 3D printer completed the first phase of a NASA technology demonstration by printing a tool with a design file transmitted from the ground to the printer, using 104 layers of plastic. The tool was a ratchet wrench.
“For the printer’s final test in this phase of operations, NASA wanted to validate the process for printing on demand, which will be critical on longer journeys to Mars,” explains Niki Werkheiser, the space station 3D printer program manager at NASA’s Marshall Space Flight Center in Huntsville, Alabama. “In less than a week, the ratchet was designed, approved by safety and other NASA reviewers, and the file was sent to space where the printer made the wrench in four hours.”
The ratchet wrench will be returned to the ground for analysis and testing, along with other parts printed in space. The 11.4 by 3.3 centimeter wrench was designed by Noah Paul-Gin, an engineer at Made In Space Inc., a Californian company that NASA contracted to design, build and operate the printer.
Images: Arno Massee Fotografie, TOBIAS SCHWARZ/AFP/Getty Images, Polaris / StudioX, REUTERS/Ahmed Jadallah, Sipa USA/ddp images, istockphoto