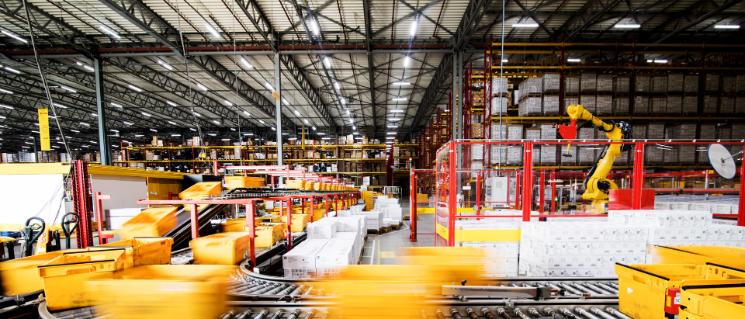
Picking smart innovations in robotics and automation
If there was ever a time to embrace smart warehouses that utilize robots and automated processes, it is now: labor shortages, social distancing measures, and amazing leaps in technology mean the warehouses of the future have arrived.
Improvisation innovation
In the complex 'new normal' that is emerging in the wake of the COVID-19 pandemic, one clear trend is a dramatic increase in e-commerce volumes. As people stayed home and retail stores were forced to close their doors, many consumers quickly turned to online retailers to stay stocked up on everyday supplies.
For DHL, the spike in demand required nimble and on-the-fly changes to many supply-chain processes. Existing efforts to digitalize the logistics sector were intensified, and new measures to ensure working in a warehouse setting was safe needed to be developed and implemented almost overnight.
As encouraging as it has been to see our company take the pandemic in stride - and find ways of helping our customers and consumers do the same - one important fact remains unchanged: there is a shortage of warehouse workers around the world. An increasing demand in e-commerce and other logistics services means warehouses are a potential bottleneck at a time when it is critical for supply chains to be running smoothly.
First robot picking cell
Hustle and bustle
Given all that goes on in a typical warehouse, it is no surprise there are not enough human hands to go around. One of the biggest tasks is 'picking' - finding a specific item in the vast space of a fulfillment warehouse. While technology such as wearables and augmented reality has made the act of picking much easier for humans, it is still very labor-intensive.
Then there are the steps associated with getting an item ready for shipment: random bin picking, co-packaging, sorting orders into put walls, and inducting objects onto conveyor belts. Finally, property mapping, surveilling and even cleaning are vital to maintaining a warehouse and ensuring it functions optimally.
There is potential to leverage automation for repetitive or physical tasks in nearly every part of warehouse operations. This frees up humans for more complex, value-adding duties. At DHL, nowhere is the progress and potential of automation and robotics on such prominent display than at our Smart Warehouse in Beringe, The Netherlands.
The smart warehouse
Beringe's Smart Warehouse encompasses 128,000 m2 of floor space. One hundred loading docks see 200-250 inbound and outbound trucks per day. But the warehouse becomes truly 'smart' when the machinery comes to life. For example, in a robot picking cell, a stationary robot handles picking tasks using machine vision technology. It can accommodate packages of all shapes and sizes, picking 600 items per hour, 24 hours per day.
Autonomous mobile robots (AMRs) work alongside humans to improve existing processes or create new ones. For example, by having robots come to workers who are performing picking tasks and transporting the goods away, the human workers spend less time on their feet moving around the warehouse and more time performing the more demanding task of picking.
By implementing wireless tracking technology, the movement of equipment and people through the warehouse can be optimized - which includes more intelligent efforts at maintaining safe social distances in the workplace.
The automated processes in place at the Smart Warehouse in Beringe are accompanied by training and certification opportunities for existing DHL employees so they can focus on doing more complicated warehouse tasks best left to humans.
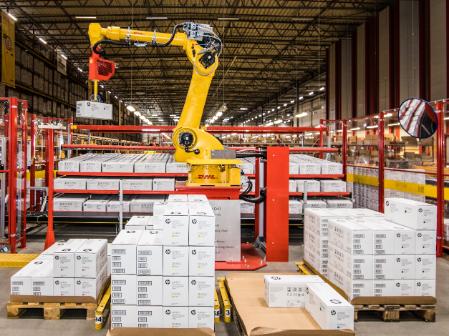
Read more about the key developments and implications in the latest edition of the DHL Trend Radar
Want it Delivered?
Why go looking for the latest logistics trends and business insights when you can have them delivered right to you?
Benefits for customers, employees, and the logistics sector
Even before the coronavirus pandemic, robots and automation had arrived in the logistics industry. DHL has been at the forefront of this trend with sites like the Beringe warehouse. With the added challenges brought on by the pandemic, automation in logistics will become even more ubiquitous.
As the importance of resilience in supply chains has become crystal clear due to the pandemic, automated processes provide a greater degree of elasticity to logistics infrastructure. Warehouse employees benefit from improved health and safety conditions while also being spared the most repetitive and strenuous tasks.
Businesses are eying the potential of micro-fulfillment, which utilizes small-scale warehouse facilities in urban areas for instant and short-time delivery to larger populations. The time and efficiency gains to be won through smart warehouse solutions mean this model is becoming increasingly viable for businesses.
As these trends continue to develop in the post-COVID-19 new normal, DHL will be at the forefront to find the best solutions for our customers, employees, and the wider logistics sector.
Published: October 2020