You are an ambitious entrepreneur with a killer idea for a small electronic device that could save your customers millions of euros a year. Impressed by your pitch, a major global company has just placed an order for 1,000 units. There’s only one catch: Your client wants to roll out the project in three months, but hasn’t quite nailed down a specification that will be compatible with its existing equipment.
Meeting that deadline looks like an impossible task. On previous projects, you’ve outsourced production to a contract manufacturer in Asia. They are fast and flex-ible, but the turnaround time for a brand-new product is still a few weeks. With the inevitable tweaks and design refinements, there’s no way you can get the units you need in the time required.
Undaunted, you make a call. Twelve hours later, a truck drops a standard shipping container at your customer’s premises. Inside, there’s a complete electronics production line, capable of manufacturing printed circuit boards, populating them with components, and assembling and testing the finished product. You -download the build instructions wirelessly, and prototype units are in the customer’s hands before the end of the day. Within a month, the mobile production facility is turning out the final design as fast as your customer can install it.
The complete package
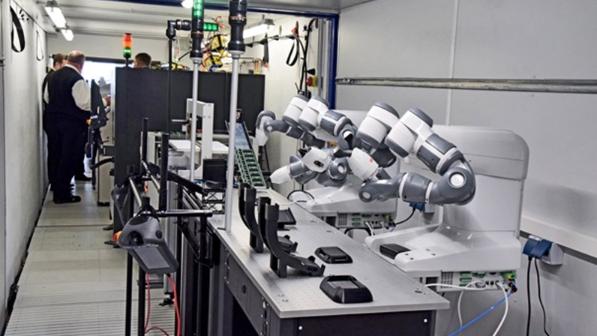
You can’t yet order up a factory like a pizza, but that’s the vision of Finnish telecoms company Nokia and a consortium of partners including DHL. The “Conscious Factory in a Box” is a working proof of concept built at Nokia’s Digital Creativity Lab in Munich. The unit, installed in a standard shipping container, includes all the equipment necessary to manufacture an electronic device. Over the last 12 months, it has traveled around Europe, demonstrating its capabilities at trade fairs and customer events.
Beyond rapid new product introduction, Nokia sees a number of potential use cases for its factory-in-a-box concept. It could help established manufacturers to rapidly restart production after a disruptive event such as a fire or natural disaster. Or it could allow manufacturers to meet country-of-origin requirements, shifting their production footprint temporarily and producing sufficient volume to meet local market requirements.
“These factories are perfectly suited to meet regional and innovation startup requirements, and can be as large as needed to meet build requirements by simply adding additional containers to the location,” says Grant Marshall, head of Supply Network and Engineering at Nokia Operations. “This is a new business model Nokia would like to offer to its customers.”
Why go looking for the latest logistics trends and business insights when you can have them delivered right to you?
Innovations in the pipeline
The idea of modular, mobile manufacturing isn’t limited to the electronics sector. The U.K. Smart Manufacturing Accelerator, a government-funded research group, has worked with manufacturer Dearman to create a prototype factory in a box for the production of tubing assemblies for truck-mounted refrigeration systems. The containerized unit includes robots and automated equipment that can cut pipes to length, bend them and braze them together. Finished assemblies undergo automated inspection and pressure testing prior to release.
The factory-in-a-box concept makes sense for this application, say the system’s sponsors, because their large size means complete pipe assemblies are expensive and difficult to transport. They envisage the system being used to aid the rollout of refrigerated transport in Africa and other emerging regions where a lack of such facilities leads to high levels of waste and prevents farmers from accessing important markets for fresh produce.
In life sciences, GE Healthcare has developed a mobile biopharmaceutical manufacturing facility designed for the production of viral vector-based therapies. This rapidly expanding approach uses genetically modified viruses to deliver genetic material to patients’ cells. The viruses are grown in special tanks before being refined and processed ready for use by patients.
GE’s biopharmaceutical factory in a box is based on the company’s KUBio platform, a scalable system of single-use processing equipment designed to meet strict industry requirements for quality control and biosecurity. The company says that its modular, mobile approach will be a boon for customers conducting late-stage clinical trials and for the production of targeted therapies aimed at relatively small patient populations.
Thinking outside the box
In reality, most factories won’t be hitting the road any time soon. The real significance of these factory-in-a-box concepts is what they say about the broader future of manufacturing. The development of highly flexible, highly capable and highly automated equipment is shifting the economics of production in important ways. By reducing the need for dedicated tooling and costly infrastructure, these approaches erode the economies of scale that have driven the development of many manufacturing sectors. They have implications for skills too. Automation, cloud computing and reliable wireless networks make it possible for manufacturers to coordinate production remotely, and reduce the requirement for specialist expertise on site. Together, those changes could allow companies to design their production networks around the needs of their end customer rather than the limitations of their manufacturing capabilities. — Jonathan Ward
Published: April 2019
Images: GE Healthcare; Nokia