Why go looking for the latest logistics trends and business insights when you can have them delivered right to you?
Stars in their eyes
Are Tesla and SpaceX simply two bold upstarts in different industries, or does something more basic bind the two companies together? With an undisputed talent for marketing, Musk has always been keen to exploit the idea of common ground between his ventures. He told journalists in 2012 that SpaceX expertise in lightweight aluminum structures had informed Tesla’s vehicle designs. The company’s flagship Model S uses the material extensively in its chassis and body. Similarly, Tesla has provided advanced battery technologies for SpaceX rockets. In 2018, a test flight of the largest SpaceX rocket to date – the Falcon Heavy – placed Musk’s personal Tesla Roadster into orbit around the sun, complete with a dummy astronaut behind the wheel.
Tesla and SpaceX also share lofty, long-term ambitions. Tesla says its mission is to “accelerate the world’s transition to sustainable energy.” Musk wants SpaceX to reduce the cost of moving people and materials into orbit by a factor of 100, and then to send people to Mars.
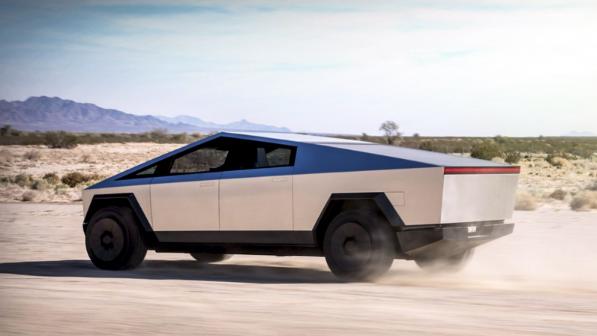
Feet on the ground
The most significant similarities, however, may lie behind the scenes. Both Tesla and SpaceX have adopted an intensely pragmatic approach to product development, eschewing their respective industry’s traditional supply chains and development approaches in the quest for higher speed and lower costs. Tesla’s battery packs, for example, are assembled from hundreds of small commodity cells, similar to those used in consumer electronics applications.
For its Starship superheavy rocket, designed to carry the huge payloads needed to support a crewed mission to Mars, SpaceX has abandoned its original plan to use carbon-fiber composites as the primary construction material. The craft will now be made from stainless steel, a material that costs around 50 times less per kilogram, is easier to fabricate, and which Musk claims will offer real performance benefits in flight.
Both companies have also absorbed the software industry’s agility, with an incremental test-and-learn approach to product development, and a willingness to reinvent products and processes if better solutions present themselves. The first three SpaceX Falcon 1 prototypes failed during launch. At the fourth attempt, a Falcon 1 became the first privately funded, liquid-fueled rocket to reach orbit. In the eight years since the Tesla Model S was first put on sale, the company’s engineers have made multiple hardware and software upgrades, with many new features and improvements made available to existing owners via over-the-air updates.
How far could they go?
“Both these companies show just what you can do if you are brave and willing to approach problems in an entirely new way,” says Fathi Tlatli, President, Global Auto-Mobility Sector, DHL. “A Tesla is perhaps more like a computer on wheels than a traditional car, and SpaceX is showing that space flight could eventually be much more like travel on the ground.”
Could Tesla’s production lines eventually be turned over to the manufacture of spaceships? The car company has already used its facilities to produce specialist tooling for its rocket-making cousin, so perhaps the idea isn’t as unlikely as it seems. More certain is that both organizations will keep experimenting, testing and evolving, making the thousands of incremental innovations that can eventually add up to truly revolutionary change. — Jonathan Ward
Published: December 2020
Images: Spacex/Science Photo Library; Tesla/Bestimage