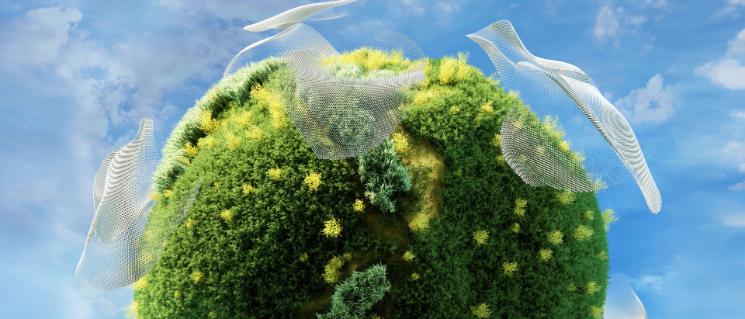
Must warehousing really cost the earth?
Changing consumer behavior has meant skyrocketing demand for logistics real estate and warehousing. But given the environmental impact of traditional warehouses, how can businesses source the space they need while meeting their sustainability aspirations?
Drive along any major highway in a developed country and you will likely see at least one in the distance by the side of the road: a huge, windowless, box-like building with trucks parked outside. The only indication of the building’s purpose is the logo of a logistics company on the side.
Warehouses – or to use the more 21st century term, distribution centers – and the land they occupy were in hot demand even before COVID-19 hit. Now, the impact of the pandemic has accelerated a permanent shift from bricks and mortar shopping to e-commerce by an estimated five years. Look no further than the food supply chain for proof: In the UK, for example, online grocery sales more than doubled in a year (from £681m to £1.44bn).
Growth at that scale calls for huge amounts of warehouse space to keep pace. An analysis from real estate experts Knight Frank shows that every billion pounds of online spend needs to be backed by 126,000 square meters of warehouse space. Knight Frank’s forecast is that UK online grocery sales online alone could require more than 650,000 square meters of warehouse space by 2024.
Physically locating that space is hard enough, but there is another, more existential challenge.
Warehousing and logistics are associated with a range of environmental impacts. These range from carbon dioxide emissions to noise and light pollution or even road safety. And with major businesses largely unified in recognizing their responsibility to helping fight climate change, nearly all have set carbon reduction targets.
So how can businesses that need warehouse space balance the responsibility of meeting consumer demand with their environmental commitments?
Zero carbon: The future for warehousing
Increasingly, developers, investors and warehouse occupants are turning their attention to incorporating renewable power and energy efficiency measures into their facilities. Net zero-carbon warehouses are the goal; investors are looking to ‘future proof’ their investment, while occupants recognize that their brand reputation is on the line.
DHL Supply Chain is committed to achieving 100% net zero-carbon warehousing by 2025. While meeting this goal is a clear priority for our business, net zero-carbon warehousing is also beneficial to our customers who can make significant reductions to their own carbon footprints by pursuing greener supply chains. Since 2008, DHL has supported customers with a broad range of GoGreen Solutions aimed at reducing their greenhouse gas emissions and improving their overall environmental performance.
Across Deutsche Post DHL Group, there are now several measures that are now standard in the Group’s approach to carbon neutral buildings.
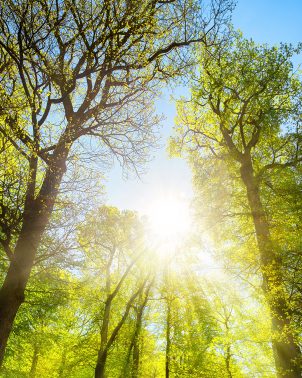
By 2025
100% Net zero-carbon warehousing at DHL Supply Chain

By 2030
90% Share of green electricity in new Deutsche Post DHL Group buildings
For example, all new buildings have a carbon neutral design, and the share of green electricity – procured from sustainable sources – will be more than 90% by 2030. By that same year, sustainably-powered sources of heating will have been rolled-out to over half of the Group’s buildings.
Locally produced electricity from renewable sources such as solar will be converted into fuel for electric vehicles, while the use of digital tools and intelligent building management systems will provide further reductions in energy consumption.
Want it Delivered?
Why go looking for the latest logistics stories and insights when you can have them delivered right to you?
Case studies: Here comes the sun
Operating a modern, technologically-advanced warehouse requires enormous amounts of energy. To optimize energy consumption in Thailand, DHL Supply Chain has invested more than $1 million in installing solar panels on the rooftops of four warehouses.
Spanning a total area of around 11,000 square meters, the panels cover a surface close to the size three football pitches. They generate enough energy to meet 38 % of the facilities’ demand, while also reducing energy use by 20 percent annually.
The initiative is just the latest in a range of recent measures aimed at increasing the sustainable credentials of the facilities and making a tangible difference in energy requirements. Others include motion sensor LED lights, which are activated only at certain times and in specific operational areas, and solar powered external lighting.
Meanwhile, a waste management initiative is helping drive customers’ businesses toward zero-waste through the principles of ‘reduction, reuse, and recycling.’
I. Bangna Logistics Campus, Samutprakarn, Thailand
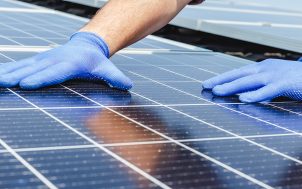
$1 MILLION in solar panels ...
covers 3 FOOTBALL FIELDS of roof space ...
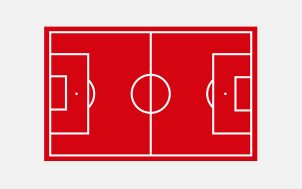
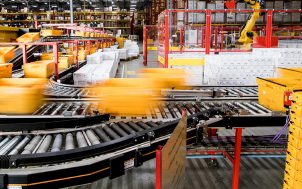
supplying 38% of energy demand.
In Australia, DHL Supply Chain began installing simple solar panel solutions on the roofs of its warehouses as far back as 2017. Since then, the team has taken that up a notch with the Urban Power Station at its HP 8 warehouse in Sydney.
The HP 8 Warehouse is a pharmaceutical-grade cold-chain site, meaning it uses a lot of electricity to keep medical products cool – all day, every day. However, it now boasts its own power plant: a 1.7-megawatt Dynamic Urban Power Station powered by 5,500 solar panels on the warehouse roof, guaranteeing 40 percent of the site’s electricity. The project was developed with partner Epho, a provider of commercial solar energy solutions. Epho’s “Bright Thinkers Power Station” (BTPS) is different from typical solutions because it includes technology that allows leftover electricity to be sold back into the power grid.
II. HP 8 Warehouse, Sydney, Australia
5,500 solar panels ...
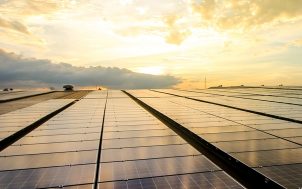
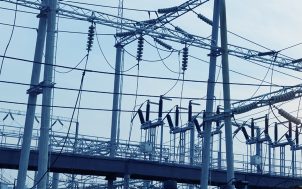
power a 1.7-megawatt power station ...
saving €180,000 per year.
The benefits of the Urban Power Plant extend beyond the smaller carbon footprint. The electricity generated is significantly cheaper than the usual coal-fired electricity commonly sold in Australia, which leads to savings of more than €180,000 a year. The excess electricity that is fed back into the grid also provides more clean power for other users in the area – helping the broader population lower its use of coal-fired electricity.
Warehouses may be unassuming buildings dotting the landscape alongside highways throughout the world, but the next time you drive by a one, keep in mind:
those e-commerce distribution centers play an important role in making logistics a more sustainable business.
Published: July 2021