The workings of the modern factory would be awe-inspiring and bewildering to a 19th-century industrialist. The average warehouse might look reassuringly familiar. Manufacturing has been transformed by successive waves of innovation, from electrification to automation and digital technologies. Most warehouses, by contrast, appear decidedly low-tech. Goods are arrayed along aisles of racking. Picking is completed mainly by hand. And the most common machine on show is the forklift truck, a device that doesn’t look so very different from the hoists and cranes that were common in the late 1800s.
It isn’t a lack of inventiveness that has kept most warehouses so stubbornly simple. Automated materials handling systems have existed since the 1960s. Yet they remain the exception rather than the rule. By 2016, for example, only 10 percent of U.S. warehouses were believed to be using any form of advanced automation in their operations.
Your inflexible friend
The Achilles’ heel of earlier generations of warehouse automation was a lack of flexibility. Conventional automated storage and retrieval systems operate best when demand is consistent and the items they handle are similar. The trouble is, that’s not how most warehouses work. Warehouses need to add flexibility to the supply chain, acting as a buffer between impatient, unpredictable customers and slow, inflexible production operations. In many warehouses, activity and inventory ebbs and flows through the year. And warehouses may store and handle tens of thousands of different items, each a different size and shape and each experiencing different rates of demand.
Recent trends, from globalizing supply chains to the meteoric rise of e-commerce, have ramped up the need for flexibility in warehouse operations. And so far, no technology has proved quite as flexible or cost effective as a human workforce.
Provided, that is, you can get the people you need. “Labor shortages are becoming an increasingly serious problem in warehouses across the world,” says Jan-Thido Karlshaus, Global Head, Technology Sector, DHL Supply Chain. And a lack of available personnel is especially problematic for operations that rely on temporary labor to cover short-term peaks in demand.
Why go looking for the latest logistics stories and insights when you can have them delivered right to you?
New partnerships
The need to find less labor-intensive ways to run warehouse operations is driving a resurgence in interest in technology, just as a range of new approaches are reaching commercial maturity. “Technology has the potential to help overcome labor-related challenges, and more importantly, to help deliver efficiency savings and ultimately better solutions to our customers,” says Karlshaus.
One key attribute of the latest generations of technologies is that they don’t seek to replace human workers entirely, but to support them in new ways. “The development of cobots that can work safely alongside people allows warehouses to add automation selectively,” says Thierry Driesens, Digital Transformation Officer, DHL Supply Chain. But, while automating parts of an existing process can be a boon for tasks that are particularly strenuous or repetitive, he notes, “The real improvements emerge when you use automation to enable an entirely new process.”
LocusBots from U.S.-based Locus Robotics, for example, are self-guiding vehicles that navigate autonomously around a warehouse carrying standard plastic tote bins. A display on the bot tells nearby warehouse associates what to pick for each bin, and a scanner confirms each item as it is loaded. By allowing workers to spend more time picking and less walking the aisles, Locus says that its system can double worker productivity. And the system handles demand variability too. When the warehouse is quiet, workers follow the fleet of bots through the facility, picking from one area at a time. At busy times, workers stay in fixed zones, and the bots come to them. Locus Robotics says that another key benefit of its system is its ability to integrate with existing warehouse operations with no need to reconfigure the racking or install fixed infrastructure.
Other advances in warehouse technology rely on digital intelligence rather than robotic muscle. DHL has partnered with leading technology companies including Cisco and Nokia to install internet-of-things technology in warehouses in Germany, the Netherlands, Poland and the U.S. These facilities use a number of different approaches, including wireless tracking technology to monitor the movement of forklift trucks and personnel through the warehouses in real time. The data collected can reveal opportunities for efficiency improvements, such as areas within the facility that suffer congestion at peak times or layouts that force associates to take circuitous routes to commonly visited areas.
Other players in the sector are ripping up the conventional rulebook entirely. U.K.-based online grocery Ocado, for example, opened a new customer fulfillment center in Andover, U.K., last year. The facility contains a three-story-high aluminum grid in which grocery items are stored in stacks of crates. A fleet of 1,100 robots moves over the grid on a 112-kilometer network of rails, lifting crates from the stack and delivering them to pick stations were employees assemble customer orders. At full speed, the center is designed to process 65,000 customer orders per week. The British company has signed agreements to supply similar technology to a number of other retailers worldwide.
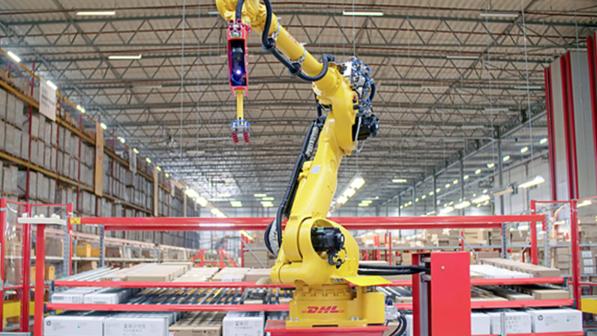
Picking up speed
If the current wave of warehouse technology is based on new collaborations between humans and machines, that doesn’t mean the dream of the fully automated warehouse is dead. Given the right conditions, the latest robot picking systems are already able to outperform human workers. DHL’s robotic picking cell in Beringe, the Netherlands, for example, uses machine vision technology to pick and stack boxes of various sizes and shapes. The system can handle up to 600 units an hour, and will operate consistently and accurately 24 hours a day.
Robots still struggle, however, when faced with chaotic or unexpected environments, such as a box containing a random selection of items of different shapes and sizes. Researchers around the world are striving to build systems that can find and pick items with the dexterity of a human being. The field took an important step forward last year when Ken Goldberg and Jeff Mahler, researchers at UC Berkeley, demonstrated the latest version of their Dex-Net system. Dex-Net is an artificial intelligence (AI) program that uses neural networks to decide how robot arms, equipped with a gripper and a suction pad, should pick up objects of arbitrary shape and size. Goldberg and Mahler say their system can pick items at a rate of 200 to 300 per hour. That’s much faster than the 95 picks managed by robots in a recent competition organized by online retailer Amazon, but still far short of the 400 to 600 that human warehouse staff achieve when faced with the same challenge.
The U.S. researchers are bullish about the prospects for the technology, predicting that robots will achieve “human or superhuman” levels of dexterity in the next five years. Even before then, it’s likely that warehouse staff will increasingly work hand-in-hand with advanced automation and AI. — Jonathan Ward
Published: April 2019
Images: DHL/Locus Robotics; DHL