Supply Chain Transformation Reduces Costs, Improves Service
Summary
As a leader in the consumer goods sector, the company manufactures a wide range of consumer goods and personal care products, which are sold in approximately 180 countries worldwide.
The company approached DHL to develop a Lead Logistics Partnership that would transform its supply chain at production facilities in Turkey, Africa and the Middle East. The LLP program focused on delivering new value through the continuous optimization, implementation and management of the supply chain. This design and management effort was complemented by day-to-day control of all transport operations and the provision of supply chain visibility of all movements both inbound and outbound.
Customer Challenge
- Disconnected supply chains across 13 manufacturing sites in the Middle East and North Africa
- Service and cost inefficiencies
- High supply chain risk caused by limited transparency
DHL Supply Chain Solution
- Design, develop and implement a fully integrated network
- Process-driven central control tower to coordinate region’s inbound operations
- Satellite control towers in all manufacturing regions
- Central Total Logistics Cost Management (TLCM) team that relentlessly identifies and delivers new value
Customer Benefits
- Improved productivity and supply chain visibility and reduced risk
- Reduction of transportation costs, transit times, inventory levels, demurrage, customs and other tax cost
- Control and reduction in CO2 emissions
- Increased On Time in Full and Case Fill Rate
Customer Challenge
The company has 13 manufacturing sites in Turkey, Egypt, Nigeria, Morocco, Kingdom of Saudi Arabia, Pakistan and South Africa. The inbound to manufacturing supply chains were completely independent of each other, thus lacking a united approach. Another challenge came from finished goods being supplied to the same region from a variety of manufacturing sites around the world. This led to a number of inefficiencies both in terms of costs and delivery time.
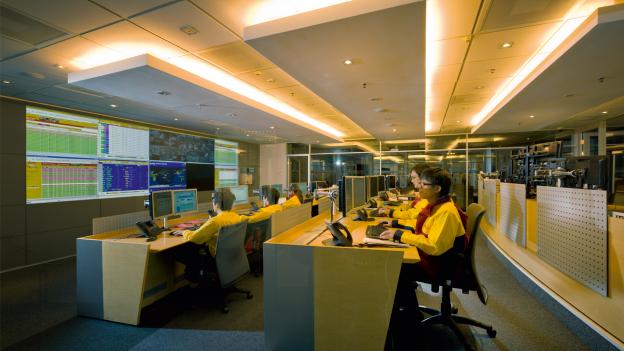
Customer Benefits
Through the LLP solution, the company has seen significant cost avoidance and savings, with a 71 % decrease in demurrage costs. There have also been improvements in service levels. Delivery on-time performance and customs on-time performance have increased by 13 % and 19 % respectively, while there has been a 32 % productivity increase on the number of FTEs within the same scope. Logistics management and process disciplines have significantly increased the percentage of “Shipment On Time in Full” (OTF), while both the right quantity and quality is delivered on the agreed delivery date. Improved Case Fill Rates reduced penalty costs that were typically incurred when containers took too long to unload. Also, an optimal and integrated network has delivered a considerable reduction in prime transportation CO2 emissions. Finally, improved customs and regulation compliance support has helped drive major reductions in transit time, inventory and overall logistics cost.
DHL Supply Chain Solution
As the Lead Logistics Partner, DHL Supply Chain developed an optimal and fully integrated regional distribution network that considered all of the customer’s regional supply chain requirements. A centrally managed control tower operation was established in Turkey with satellite control towers in each country of manufacture. Operations are managed and controlled with a web-based DHL Transportation Management System. The central team looks after order planning, supplier management, load planning, carrier management, booking, and event updates, along with track-and-trace. Meanwhile teams in each manufacturing country work closely with the local customer to ensure a fully aligned and consistent approach and take care of the final stages of the logistics process, including customs management.
Customer Benefits
Through the LLP solution, the company has seen significant cost avoidance and savings, with a 71 % decrease in demurrage costs. There have also been improvements in service levels. Delivery on-time performance and customs on-time performance have increased by 13 % and 19 % respectively, while there has been a 32 % productivity increase on the number of FTEs within the same scope. Logistics management and process disciplines have significantly increased the percentage of “Shipment On Time in Full” (OTF), while both the right quantity and quality is delivered on the agreed delivery date. Improved Case Fill Rates reduced penalty costs that were typically incurred when containers took too long to unload. Also, an optimal and integrated network has delivered a considerable reduction in prime transportation CO2 emissions. Finally, improved customs and regulation compliance support has helped drive major reductions in transit time, inventory and overall logistics cost.