DHL SUPPLY CHAIN EXPANDS ITS FLEET OF ROBOTS FROM 6 RIVER SYSTEMS
Press Release: Praha, September 1, 2022
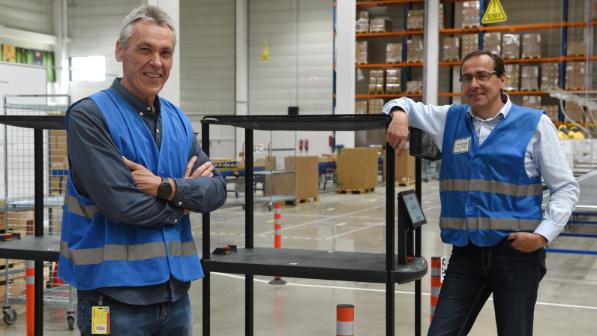
- Assistant picking robots from 6 River Systems help workers in DHL Supply Chain warehouses in the Czech Republic and other European countries
- After the successful automation of the warehouse in Pohořelice, picking robots are also coming to the distribution center in Jirny
- DHL Supply Chain already uses almost 30 robots from 6 River Systems in the Czech Republic
DHL Supply Chain, a leading provider of contract logistics services, continues to automate and digitize its warehouse operations. After the successful deployment of assistance picking robots from 6 River Systems in the warehouse in Pohořelice, the collaborative robots will now also help the employees of the distribution center in Jirny. Since the peak season in both warehouses starts at different times, the main advantage of these automated solutions comes into play. Given the relatively easy “plug and play” installation of the robots, both operations in Pohořelice and Jirny can shift robots between the warehouses according to current order volume and needs. Almost 30 assistance picking robots from 6 River Systems are currently operating in the Czech warehouses of DHL Supply Chain.
“We have strengthened the technical arsenal of the distribution center in Jirny by ten new robots, and we can count on a few additional robots during seasonal peaks. In addition, we will be able to use robots from the pan-European fleet of DHL Supply Chain in Jirny. The assistant picking robots from 6 River Systems are flexible and can be moved between our operations,” says Vladimír Kvítek, Business Unit Director DHL Supply Chain, adding: “These are the same robots that we put into operation in the Leder & Schuh warehouse a few months ago. Robots do not take people's work, but on the contrary help them and significantly speed up and simplify the entire process of picking goods and completing orders.”
The 6 River Systems assisted picking robots are intended for picking e-commerce orders. “By using robots, we can increase human productivity by 30%, which allows us to use our well-trained human workforce much more efficiently elsewhere,” explains Ivo Zdvořáček, who is in charge of implementation at the distribution center in Jirny. “Robots move faster, and people, when they don’t have a load and don’t have to push anything, also move more nimbly. This significantly speeds up the entire order picking process. In addition, collaborative robots improve the working environment for our employees.”
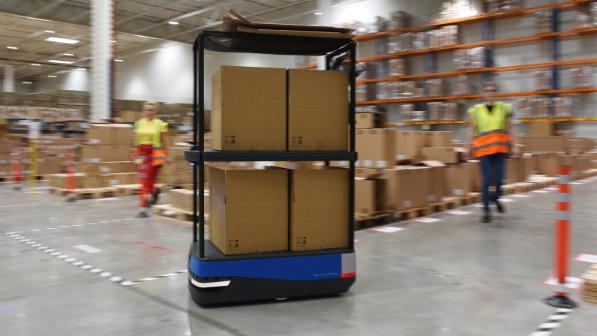
The Jirny robots are autonomous but require human assistance. They travel between the aisles and carry the products picked, while the actual picking from the shelves is still done by human workers. However, this also happens smoothly and with the support of intelligent technologies. The employees of the distribution center in Jirny also benefit from the intuitive “pick by light” method. This means that a light shows the operator which box to pick. The corresponding box is also illuminated from below with LEDs. Even an untrained worker can thus perform at highest-quality levels. In addition, the process of training new employees is accelerated. Instead of several days of training, people learn to work with the robot within an hour.
The robot moves around the warehouse completely autonomously using an electronic map, which is manually compiled by 6 River Systems technicians during implementation. Using radar sensors, the robot can recognize obstacles and go around them at a sufficient distance, so it meets very strict work safety conditions. It also determines when it will go to the charging station, depending on the state of charge of the battery pack and the work schedule. At the starting point, the robot receives information and cartons into which the required goods are picked. From here it continues to one of the contact points depending on the order being picked. Here, an operator picks up the robot and completes the appropriate route around the warehouse with it. After picking all the items, the robot transports the goods for further processing to shipment.
The new robots immediately fit in perfectly with the work team in Jirny. “We even named the robots with nicknames,” says Vladimír Kvítek. “We made a poll among the 1,200 employees of the distribution center, and people gave the robots names of Greek gods. In the same way, we have previously named palletizers and other automation technologies, a simple solution which increases the acceptance of these technologies with our employees. Before their introduction into operation, we communicated intensively with the employees. From the beginning, we created a group of key users, which we involved in the entire project from its preparation to implementation. That way, people had enough time to get used to the robots and absorb the change. They were part of the whole implementation. In addition, our employees appreciate the help of robots, especially at a time when there is a shortage of workforce,” concludes Vladimír Kvítek, who is currently working with his team on a project to implement another helper – a robotic arm that palletizes and is mobile for use in various operations.