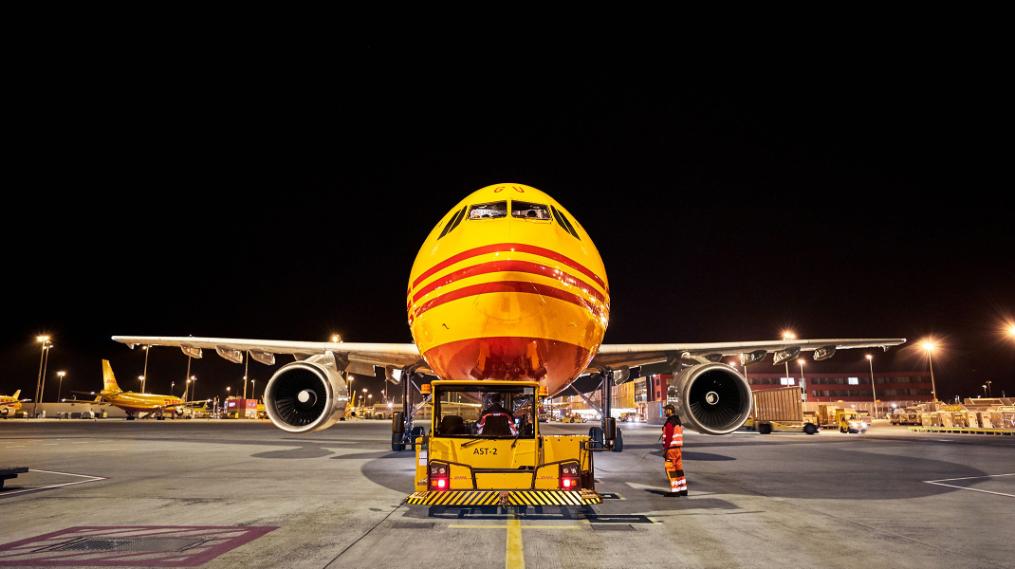
Logistics Use Cases: Shipment Focus
Dimensioning Application
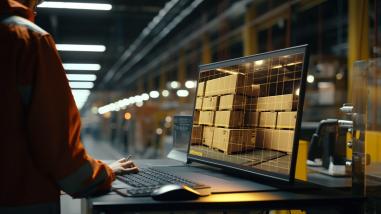
It’s essential to accurately measure either the area or the volume occupied by an object before shipping. Dimensioning enables capacities to be calculated for storage, handling, load utilization planning, and transportation of goods, as well as for shipment billing. And dimensioning helps to optimize the master data on which each warehouse management system (WMS) operates.
The time dimensioning takes is critical. For example, DHL ships millions of various-sized packages a day, most travelling at fast speeds on a conveyor belt, so even a momentary delay in understanding their sizes is likely to significantly stall progress. And not just for speed but also for optimal packaging planning and better use of materials, it is very important to identify odd-shaped parcels mixed in with regularly shaped ones.
The dimensioning process can be automated with computer vision technology, in different types of systems. A fixed system such as the MetriXFreight solution from the German software company Metrilus can continuously monitor a defined measurement area for goods. It starts dimensioning whenever an item arrives at the measurement area from any direction, regardless of orientation and exact positioning.
Based on a handheld terminal, the California-based software company Qboid offers a mobile dimensioning solution that integrates advanced 3D color sensors and computer vision algorithms. This enables the automation of dimension and shape estimation tasks in more types of items than is possible with a traditional system.
Challenges of Implementation
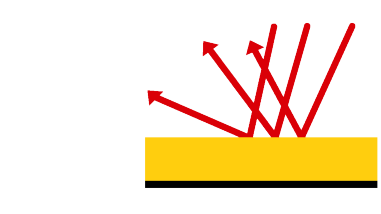
Challenge 1: Shiny objects cannot be accurately measured, as reflective surfaces and transparent materials that bounce back light pose a challenge for dimensioning technologies.
Challenge 2: Extremely large objects and extremely small objects are difficult to measure with automatic dimensioning systems.
Challenge 3: Accuracy depends on the position and resolution of the camera used in for dimensioning.
Compliance Applications
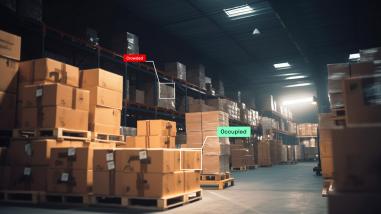
Quality Inspection
When thousands of items of various types, sizes, and shapes are passing through a facility every day, it may not be that easy to spot a damaged item. But if a box is wet, ripped, or bent out of shape, and the products inside are also spoilt in some way, this can jeopardize brand image and reduce consumer satisfaction.
The important thing with shipment quality inspection is to detect damage early on. If a damaged item passes through the facility, it will likely be labeled and assigned a delivery location. This will make it difficult to trace and redirect, as the damaged item will need to be retrieved, repackaged, relabeled, and rerouted.
US manufacturer of machine vision systems, Cognex offers an advanced dimensioning solution that includes damage detection. With a 3D and 2D camera system, it automatically detects damage to boxes such as open flaps, dents, bulges, and crushed parts. It eliminates manual re-routing, enables early intervention, and keeps the shipment line moving efficiently.
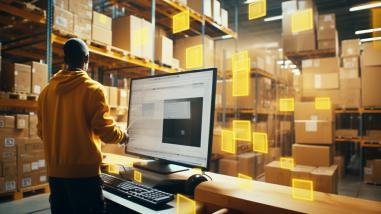
Label Detection and Alignment
Consumers are unlikely to buy a food or beverage product or use medication if the label is missing or illegible. Typically, companies are legally obliged to provide a list of ingredients, nutritional information, and a ‘best before’ date with these products and more. Country compliance laws may also require allergen labeling, recyclable materials labeling, and more. Companies can lose money and even face legal action for a bad batch of labels.
Computer vision-based systems can read labels, capturing front and back images of packaging before shipment. This visual data is processed to ensure individual product labels match a master image. Some systems also include an expiry date check system.
If errors or anomalies are detected in the text and graphics of the label itself – maybe the ink is smudged or the label is wrinkled or misaligned – or if a product has been mislabeled, the AI-powered system can trigger a reject mechanism. Detecting label damage early helps to speed up resolution. The item can be extracted from the goods flow and promptly relabeled, resuming its journey in the shortest space of time.
A computer vision system can also identify labels that have been applied to hazardous materials, using this visual information to automatically reroute those items to be repacked in compliance with any hazardous materials shipment requirements. Similarly, it can identify labels on high-priority shipment items that must be delivered to customers within an agreed timeframe. The Denver-based computer vision startup Visionify offers label checking solutions to ensure a smooth shipping process. These can verify labels on cartons, boxes, and bags of all sizes, shapes, and orientations, whether the item is stationary or in motion.
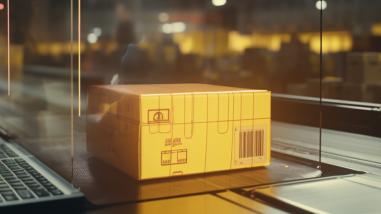
Barcode Scanning and OCR Capture
Automated product identification takes numerous forms. Barcode lines, dots, and spaces have become a familiar sight by the early 1980s. More recently optical character recognition (OCR) has enabled information from scanned documents and images to be converted into machine-encoded text.
Computer vision systems that adopt barcode scanning and OCR capture can effectively replace time-consuming manual barcode scanner and data input.
PepsiCo uses an advanced AI-powered platform solution from KoiReader Technologies and NVIDIA to enable greater efficiency in reading warehouse labels and barcodes in its fast-moving environments. Labels can be any size, at any angle, and even partially obstructed or damaged. Also, the technology company Banner offers a range of innovative solutions in this field. These can decode difficult-to-read, low quality, and damaged barcodes, and even codes printed on highly reflective surfaces.
The Belgian technology company Zetes specializes in solutions for supply chain optimization and offers computer vision systems for shipping and loading verification. These can capture a full view of loaded pallets, detecting and decoding multiple barcodes simultaneously and comparing this data to shipping orders. Operators receive real-time alerts about discrepancies and missing or unreadable barcode labels. Camera gates can then capture images of every pallet, and the system decodes and verifies pallet barcodes, triggering a go/no-go signal for the loading operator. Proof of loading is provided by time-stamped images.
Challenges of Implementation
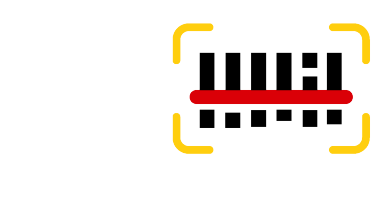
Challenge 1: Environmental factors can be a challenge for barcode reading. Under poor lighting, shadows, or reflections, algorithm accuracy decreases.
Challenge 2: Not all handwritten labels can be read by OCR technology and it may be impossible to scan greasy or torn barcode labels. Manual data entry may sometimes be needed.
Shipment Localization: Automatic Sorting
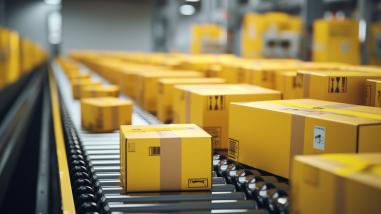
Shipments need to be identified before being sorted according to their type and destination of delivery. This visual classification process can be slow and tedious for workers, and can cause a bottleneck, so it is critically important to automate these tasks. AI and neural networks can be used to segment and pinpoint the location of parcels, envelopes, bags, and more and to accurately determine the placement and alignment of these items.
Camera-based automated sorting systems are used to accelerate the sorting process, and the best results are achieved when utilizing high-quality 3D data. These systems distinguish the different characteristics of each item to enable object classification and quality evaluation. As items arrive on the conveyor belt, they are uniformly separated, spaced, and aligned (a process called singulation). Cameras capture images of each item, which are recognized by AI-powered technology. The known item is then directed to the correct bin or onto another conveyor belt for further sorting.
This type of computer vision system matches the image and the sorting decision in real time, and there are three steps to achieving the sorting decision: first, the captured image is converted to a binary image, next product edge detection is applied, and then the result is matched with the base image.
Combining a PhoXi 3D scanner and localization as the eyes of the system and AI algorithms as the brains, Photoneo has achieved an advanced singulation and sorting solution based on a pre-trained neural network that can recognize parcels for pickup with 95% accuracy. It can pick up solid objects with deformed surfaces that change under the slightest pressure, doing so in cycle times of less than 1.3 seconds for throughput of 2,500 non-standardized objects per hour.
Challenges of Implementation
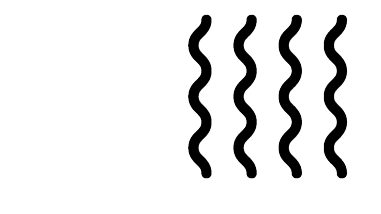
Challenge 1: Not all computer vision singulation systems can handle shiny surfaces.
Challenge 2: It is difficult to achieve fast, accurate automated sorting of disorderly stacked parcels.