The Four Most Common Shipment Hazards
How to protect your cargo from them
You can help prevent damage to your goods during transit using a variety of measures. Packaging is an important part of limiting the potential impact of the common hazards shipments face in air and ocean transportation.
The Most Common Shipment Hazards
It is easier to know how to adequately package and secure your goods if you understand the risks you are protecting them from. While we explored key handling requirements for your cargo in a previous article, the most common hazard for regular (non-hazardous) products during transit are:
- Punctures & Abrasions
During air transportation shipments are co-loaded with other commodities in trucks and shipping containers. Punctures and abrasions can occur when the shipment comes in contact with other cargo. This can also be the result of improper or insufficient internal packaging that does not prevent the contents from shifting/falling pressing through the exterior packaging. - Compression
Compression/crushing is the result of co-loaded cargo being loaded on top of a shipment. Unsupported exterior packaging can give way causing damage. Inner packaging must be configured to the product or dunnage used to fill the open spaces. This provides firm support to the exterior packaging and reduces the opportunity for compression. - Environmental Exposures
Climate and geography can be significant contributors to product damage. Excessive moisture or water can not only damage a shipment’s contents, it can also effect the integrity of the packaging. Adhesive used in corrugated cardboard boxes can be softened by moisture fall apart in transit. - Shipment Handling
An air shipment will experience more than 8 touch points while in transit. Heavy shipment (over 150 lbs / 70 kgs) that are not palletized, requiring manual lifting, have increased exposure to drops and sliding. Palletized shipments not properly secured properly or balanced can slide or tip while being moved by the forklift. - Shock
An air shipment travels on multiple modes of transportation to move it from the shippers dock to the customers door; trucks, forklift, conveyors, airport dolly carts, etc. These modes of transportation will introduce the possibility of shock to the packaging. Damage can occur if the inner or exterior packaging cannot withstand the handling elements that a shipment encounters while in transit.
Get Logistics Insights by Email
Subscribe to our monthly market updates and get invited to exclusive webinars where our Freight Forwarding Experts answer all your questions on global trade.
Securing Your Goods
Banding and shrink-wrap are the two primary methods of securing goods to a pallet and should be employed for outsize or palletized shipments. The types of banding to be used can include steel, nylon, polyester (PET) and polypropylene. Metal is more suited to heavier solid items whereas nylon and PET are recommended for boxes and lighter items. If using plastic strapping, ensure that it is highly durable and will create an unbreakable seal.
Shrink Film/Shrink-wrap
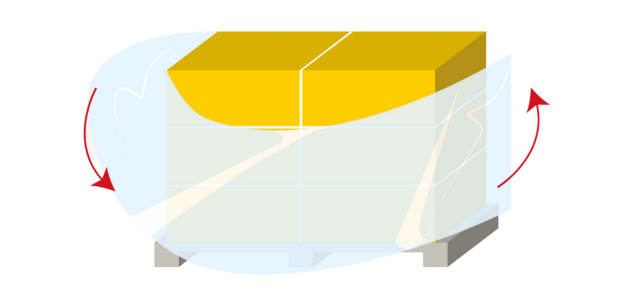
- To apply shrink-wrap, secure the leading edge of 70 gauge stretch or shrink-wrap to the pallet or forkable base.
- Apply the shrink-wrap by tightly rotating the film horizontally around the goods.
- Continue applying the film upwards whilst ensuring a 50% overlap on the previous layer of film.
- At the top, diagonally crisscross the film from each corner until the top is fully covered.
- Finally, angle the film downwards and apply a tight overlap around the base of the pallet.
Banding/Strapping
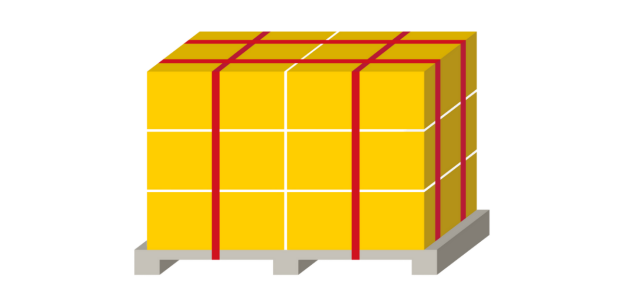
- When applied correctly, strapping is an ideal way to secure your shipment.
- Banding / Strapping should always be 4 ways (vertical) per IATA standard
- If manually applying the strapping, loop the first piece underneath the pallet void and over the top of the goods to secure it vertically.
- Repeat the strapping in all directions so that at least four straps tightly secure the load.
- Use horizontal edge protectors to avoid bands cutting into edges of the top boxes.
- Use shrink-wrap to further protect the shipment from environmental damage during transportation.
Edge Protectors
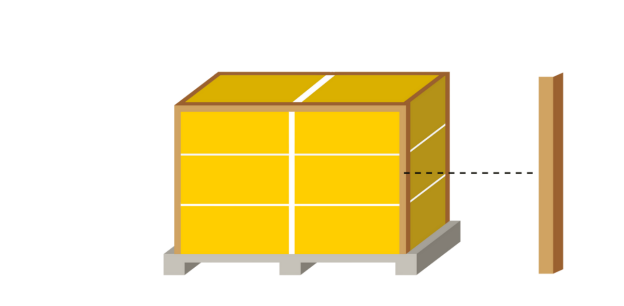
- Vertical edge protectors not only reduce damage to box edges during transport but also help to stabilize the load. Horizontal as well as vertical edge protection is advised. Vertical edge protector should extend from the top all the way to bottom, touching the skid.
Overpack or Paperboards
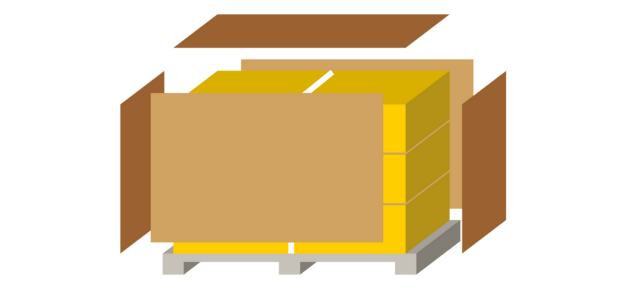
- Paperboards positioned on the top, base and sides provide a protective barrier. They help to spread the weight of shipments placed on top of and against the base slats of the pallet.
Bracing
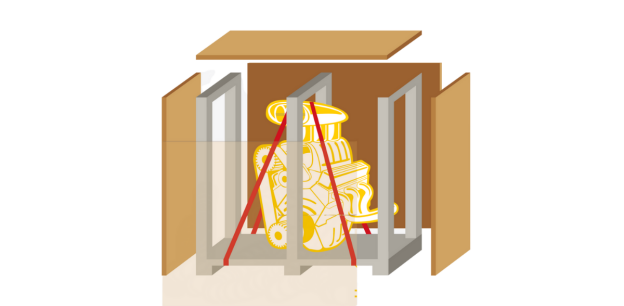
- When shipping outsize pieces such as cable reels or engines, ensure that the items are braced against the pallet with wood or metal. The bracing should prevent sideways movement that may occur during transportation.
Pre-Shipment Testing
It is highly recommended that shippers conduct some type of package performance test to verify the effectiveness of its packaging. Testing will determine if it will withstand the normal rigors of transportation and protect its contents (product). The primary advantage of pre-shipment performance testing is it provides the opportunity to evaluate the product protection performance of the packaging and to make any necessary changes to the packaging prior to a larger implementation.
Conducting pre-shipment performance tests in a laboratory setting will assist in evaluating the package’s ability to protect the product from the common hazards encountered during transportation. When determining testing protocol, remember that shock, compression, handling, vibration, and environmental exposures can all have very different effects on your packaged product, so the testing should focus on all variables.
You Might Also Be Interested In
Want to Read More Freight Forwarding Stories?
Get the latest on Air, Ocean and Rail Freight Forwarding in your inbox every month, along with regular invitations to our webinars.