
Examples
Multi-shoring the Supply Network
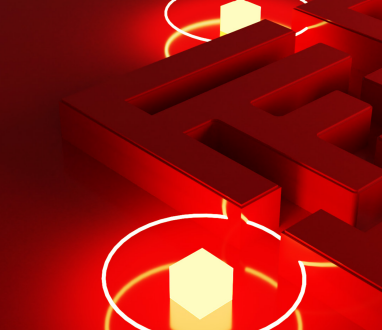
As outlined in Chapter 2, the first dimension of supply chain diversification is geographic and can range from a supply network built on one country or region to one widely dispersed across multiple regions or continents.
The multi-shoring trend is particularly evident in the manufacturing of electric vehicle (EV) components as companies expand their capabilities. Volkswagen Group (VW) provides a best-practice example with PowerCo, which was established to bundle the group’s activities along the EV battery supply chain. VW is now building gigafactories strategically located in key markets in Europe and North America.3 This allows the company to mitigate risks, respond rapidly to market demands, optimize costs, and meet sustainability goals. Another example is Geely-owned Swedish car manufacturer Volvo, which is investing around €1.2 billion in a new EV plant in eastern Slovakia, the first new European production site for Volvo Cars in almost 60 years.4
In 2022, LEGO Group announced plans to invest more than US$1 billion in a new factory in Chesterfield County, Virginia, their first in the United States and seventh factory globally.5 The company has served the North American market from their site in Mexico. LEGO Group says that they position their factories close to their biggest markets to shorten the distance their products must travel, allowing the company to rapidly respond to changing consumer demand and better manage their carbon footprint.
After years of manufacturing most of their products in China, many technology companies are now seeking to add manufacturing capabilities elsewhere, mainly in other Southeast Asian countries, often referred to as the “China+1” strategy. For example, HP is shifting its laptop production to Thailand, and Foxconn is moving a portion of its assembly capabilities from China to Vietnam.6 Tech-giant Apple is also shifting production from China, where currently most iPhones, iPads and other Apple products are produced, to India, Vietnam, and other Asian countries. Apple now builds around 14% of its iPhones in India, twice the amount it produced there the previous year.7
Furthermore, Google is diversifying its geographical manufacturing footprint by adding production of its Pixel in India and Vietnam next to existing factories in China.8 Dell has also updated its sourcing strategy to better meet market demands. In response to challenges like the semiconductor component shortage, Dell instructed its suppliers to significantly reduce their use of Chinese-made chips and components, even if sourced from non-Chinese companies. The company plans to make at least 20% of all its laptops in Vietnam this year. This multi-shoring approach helps Dell enhance its resilience during supply shortages.9
These strategic decisions are designed not only to reduce dependencies and increase resilience but also to bring organizations closer to a vast and attractive customer base and access large, skilled labor pools, such as those in India.
Multi-sourcing the Supply Network
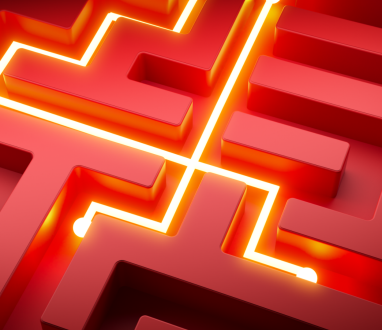
The second dimension of supply chain diversification mainly involves adding redundancies in the supplier base, i.e., additional suppliers for the same parts or products. Although multi-sourcing is not a new concept, and companies across all sectors continually assess and adapt their supplier bases, there has been a noticeable increase in recent years driven by higher supply chain volatility. The 2022 EY Industrial Supply Chain Survey found that 62% of industrial companies surveyed had made significant changes to their supplier base in the previous 24 months and 77% had or were planning to increase their total number of suppliers.10
One of the world's largest fashion groups provides a prominent example of a business effectively leveraging multi-sourcing on a global scale. The company strategically spreads their supply chain across thousands of facilities and direct suppliers worldwide. This strategy allows the company to adapt swiftly to peak customer demand and leverage the unique strengths of each supplier. Multiple suppliers also mean they can respond quickly to disruption, redistributing production to ensure products are always in stock.
A European elevator producer and the leading construction and mining equipment manufacturer provide additional examples of how multi-sourcing strategies can lead to increased customer centricity, flexibility, and resilience. The global leader in the elevator and escalator market purchases the same supplies from multiple suppliers to ensure product availability and agility, allowing the company to respond quickly to market needs. The leading construction and mining equipment manufacturer follows a multi-sourcing approach for technical supplies, which balances orders across suppliers, improving time to market. Redundant part suppliers have improved the company’s resilience and competitive advantage, reinforcing their leading market positions.
Adding Transport Modes
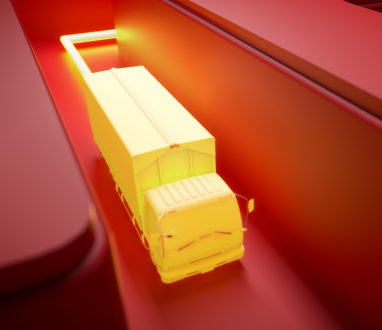
The third dimension of supply chain diversification concerns the physical flow of goods. Adding modes of transport can decrease interdependencies, fostering agility and resilience and boosting a company’s overall value proposition.
A retail market leader provides a best-practice example of this dimension of supply chain diversification. Aiming to respond rapidly to consumer preferences and trends within 10 to 14 days, the company utilizes all modes of transport across all supply lines, opting, for instance, to ship goods via air freight between regions rather than using slower ocean freight. This allows swift and flexible stock reallocation between markets based on customer requirements and disruptions.
A global technology company presents another excellent example of utilizing additional modes of transport to improve market responsiveness and flexibility, control costs, and lower emissions. The company leverages a combination of air freight for critical shipments and ocean freight for build-to-stock shipments and bulkier goods. They also take advantage of fast ocean freight services from China to the United States (14-day transit time), with the option to fly express shipments if needed, which enhances flexibility tremendously.
A leading pharmaceuticals and medical device company offers an additional perspective on the benefits of diversifying the mode of transportation. The company tailors its transport mode strategy to product and market requirements. Although air freight is often necessary, they increasingly utilize ocean and road transport to diversify their supply chain, reduce costs and minimize emissions. This diversification allows the company to adapt quickly to market needs. For example, the firm traditionally relied on bulk shipments due to a high demand for products that didn’t require temperature monitoring. With the recent increase in biopharma products, there is an emerging need to transport more low-volume shipments of temperature-sensitive products. In response, the company adapted its supply chains to include temperature-controlled options.
Diversifying Logistics Operations
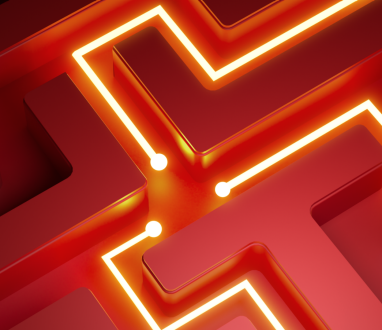
The fourth dimension of supply chain diversification focuses on expanding logistics infrastructure to provide alternative options that maintain continuity in the supply chain during disruptions. A global sportswear and athletic equipment manufacturer provides an excellent example of a company transitioning from a centralized to a decentralized and diversified logistics network. While the company aims to optimize profitability, the goal of its supply chain strategy is also to improve resilience. They deliver products from production sites directly to regional and local warehouses, enhancing resilience and cost efficiency. The company has also increased its logistics footprint, establishing a presence in South America and India, opening a new hub in Southern Europe, and expanding operations along the east and west coasts of the United States.
An European elevator manufacturer and a global productivity partner for mining and construction employ a similar logistics diversification strategy but on a regional scale. Each company assembles different parts of its finished products at separate distribution centers across several regions. Spare parts are stored primarily at each country’s local distribution and customer centers, facilitating rapid repair of essential products as needed. Finished products are shipped directly from production sites to customer centers to ensure customer centricity and agility.
Ready to diversify? Check out our implementation recommendations.