Navigating the World of Shipping: Your Guide to Dry Bulk Liners
Everything You Need to Know About Dry Bulk Liners for Efficient and Cost-Effective Transportation of Dry Cargo
Dry bulk liners are a game-changer for shippers of dry cargo, providing a more efficient and cost-effective way to transport goods. These liners are available in different types, produced from PE (Polyethylene) or PP (Polypropylene) materials with bespoke designs catering to the varying needs of shippers.
Why Use a Dry Bulk Liner?
Using dry bulk liners is a win-win solution for shippers and their customers, providing a cost-effective, environmentally friendly, and high-quality way to transport dry cargo. Whether you transport agricultural, petrochemical or other cargos, the benefits of using a dry bulk liner are significant and worth considering:
What Cargo Is Commonly Shipped in Dry Bulk Liners?
To transport cargo efficiently and cost-effectively, choosing the right solution is crucial. If the cargo quantity falls below or above these ranges, it might require smaller packages or bulk vessel solutions.
The versatility of dry bulk liners allows for the transportation of cargo from different industries, making it an ideal choice for various products like food, chemicals, and minerals. You can use dry bulk liners to transport cargo from a variety of industry sectors, including:
What Are the Different Types of Dry Bulk Liners?
There are two primary types available in the market: PE and Woven. You can install these liners in various configurations into standard container sizes, such as 20’, 30’, 40’, 40’OT, and 45’, including Bulktainers commonly used for Intermodal transports.
Depending on the nature of your cargo, you may need fluidizing pads to help with efficient discharge of less flowable cargo. The liners come with different specifications of openings that can be incorporated, and different bulkhead systems are available. The most common bulkhead system is horizontal bars across the door end.
Woven liners
Woven liners are ideal for heavy items that require robust performance for high-speed loading. They have high modulus, which gives them a high level of stiffness and strength to carry weighty loads.
As a result, they are incredibly durable, making them ideal for use in demanding and high-stress applications.
Woven Liners Pro’s:
- High modulus – robust performance for high-speed loading of heavy items
- Cost effective solution for non-critical food safety and general cargos
- Breathable – allows products with high moisture content to breathe
- Material is recyclable
PE Liners
PE liners are food-grade with no fibers, making them ideal for critical applications. They provide a moisture barrier that prevents free-flowing cargo from caking or spoiling. You can equip them with an oxygen barrier for sensitive cargo.
Additionally, they are transparent, allowing you to view the product and ensure that all residues are removed.
PE Pro’s:
- Food grade with no fibres makes the material ideal for critical applications
- The material provides a barrier to moisture barrier to prevent free flowing cargos from caking / spoiling. Can be equipped with an oxygen barrier for sensitive cargos
- Transparency allows product to be viewed to ensure all residues are removed
- Material blends can be varied to contend with abrasive materials
- Material is recyclable
Woven liners
Woven liners are ideal for heavy items that require robust performance for high-speed loading. They have high modulus, which gives them a high level of stiffness and strength to carry weighty loads.
As a result, they are incredibly durable, making them ideal for use in demanding and high-stress applications.
Woven Liners Pro’s:
- High modulus – robust performance for high-speed loading of heavy items
- Cost effective solution for non-critical food safety and general cargos
- Breathable – allows products with high moisture content to breathe
- Material is recyclable
PE Liners
PE liners are food-grade with no fibers, making them ideal for critical applications. They provide a moisture barrier that prevents free-flowing cargo from caking or spoiling. You can equip them with an oxygen barrier for sensitive cargo.
Additionally, they are transparent, allowing you to view the product and ensure that all residues are removed.
PE Pro’s:
- Food grade with no fibres makes the material ideal for critical applications
- The material provides a barrier to moisture barrier to prevent free flowing cargos from caking / spoiling. Can be equipped with an oxygen barrier for sensitive cargos
- Transparency allows product to be viewed to ensure all residues are removed
- Material blends can be varied to contend with abrasive materials
- Material is recyclable
Get Logistics Insights by Email
Subscribe to our monthly market updates and get invited to exclusive webinars where our Freight Forwarding Experts answer all your questions on global trade.
How to Ship Dry Bulk Liners End-To-End?
The shipping process for dry bulk liners can be complex, with multiple steps involved in ensuring safe and efficient transport. From selecting the appropriate carrier to managing documentation and customs requirements, there are various considerations to consider. Here are the steps involved in shipping dry bulk liners from end to end:
It is crucial to follow these steps to ensure a smooth and efficient shipping process for dry bulk liners.
How to Load and Unload Dry Bulk Liners?
Loading and unloading dry bulk liners requires careful consideration to ensure safe and efficient cargo handling. Therefore, it's crucial to assess the loading and unloading sites before shipping to determine the best approach. By working with experienced professionals in dry bulk engineering, you can ensure a safe and efficient loading and unloading process for your cargo. Whether you're shipping food products, chemicals, or other dry bulk materials, consider partnering with a reliable and experienced provider to ensure your cargo arrives safely and on time.
For turnkey solutions, engineering companies specializing in dry bulk can provide customized loading solutions based on the site's product characteristics, storage, and EHS requirements. There are two primary types of loading solutions depending on the position of the container:
- Horizontal Position: When the container is in a horizontal position, you can choose from various loading methods, including pneumatic system loading (using pressurized air), belt throwers, belt conveyors, and screw conveyors.
- Tilted Position: Alternatively, if the container is in a tilted position, it allows to gravity-load your commodity to maximum capacity.
With unloading your dry bulk liners, the consignee's input is essential to ensure a smooth and hassle-free process. You'll need to let them know where you want the cargo delivered so they can advise on the best unloading method. There are two standard options available:
- Tilting Chassis: Unloading with the container on a tilting chassis that has a built-in system.
- Usual Chassis: Unloading with the container on a usual chassis onto a tilting platform with equipment on-site.
For turnkey solutions, engineering companies specializing in dry bulk can provide customized loading solutions based on the site's product characteristics, storage, and EHS requirements. There are two primary types of loading solutions depending on the position of the container:
- Horizontal Position: When the container is in a horizontal position, you can choose from various loading methods, including pneumatic system loading (using pressurized air), belt throwers, belt conveyors, and screw conveyors.
- Tilted Position: Alternatively, if the container is in a tilted position, it allows to gravity-load your commodity to maximum capacity.
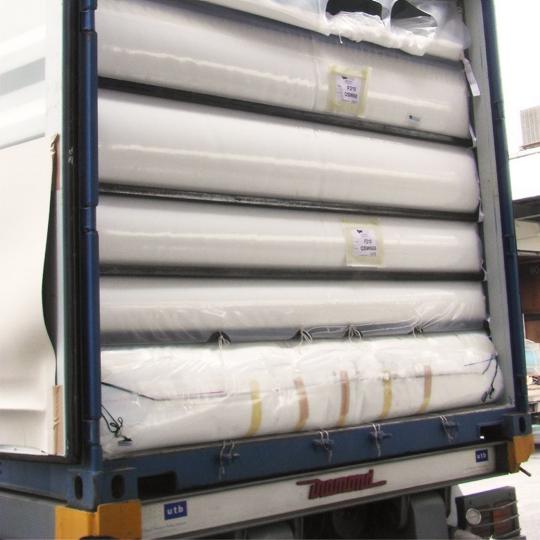
With unloading your dry bulk liners, the consignee's input is essential to ensure a smooth and hassle-free process. You'll need to let them know where you want the cargo delivered so they can advise on the best unloading method. There are two standard options available:
- Tilting Chassis: Unloading with the container on a tilting chassis that has a built-in system.
- Usual Chassis: Unloading with the container on a usual chassis onto a tilting platform with equipment on-site.
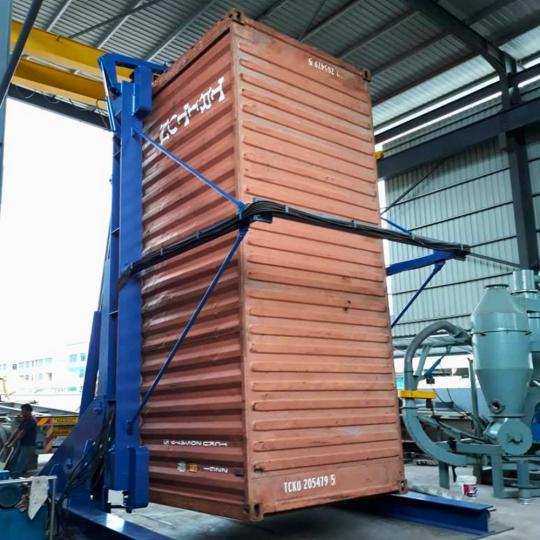
What Happens With a Dry Bulk Liner After the Discharge?
Before transportation, choosing a dry bulk liner made from recyclable materials will minimize your environmental impact. But when it comes to dry bulk liners, what happens after the discharge is just as important as the transportation itself. Here are some key considerations:
Top Tips When Shipping Dry Bulk Liners
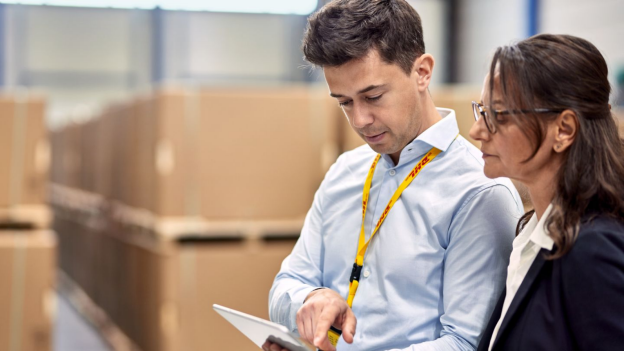
1. Evaluate the potential benefits of dry bulk liners
Such as reduced handling, optimized transport costs, and less packaging waste. Then, compare these benefits with your existing modes of transport to make an informed decision.
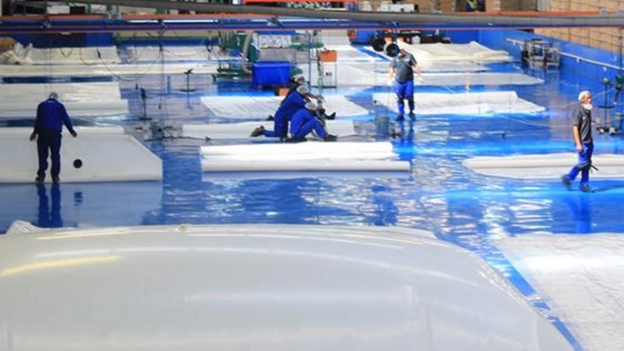
2. Assess the entire door-to-door operation
Including the recovery of the liner for recycling, to ensure that it aligns with your requirements.
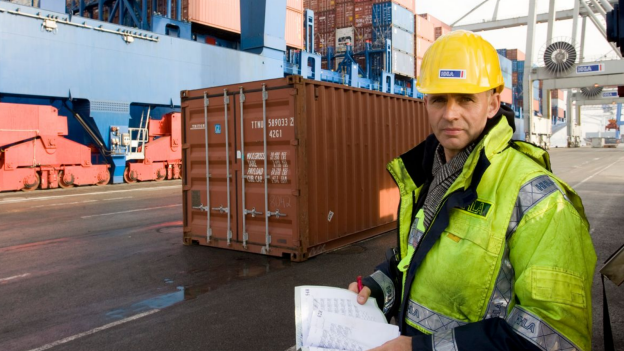
3. Evaluate the loading and receiving sites
Seek support from specialized engineering companies to design the most suitable loading solutions based on product characteristics and EHS requirements.
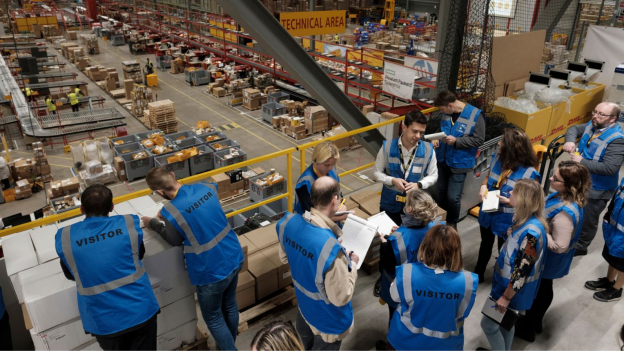
4. If you're using a 3rd party terminal for loading…
… Ensure that they have proper processes in place for receiving, storing, and loading your cargo into a container. Also, remember to evaluate EHS requirements for safe storage, loading, and unloading.
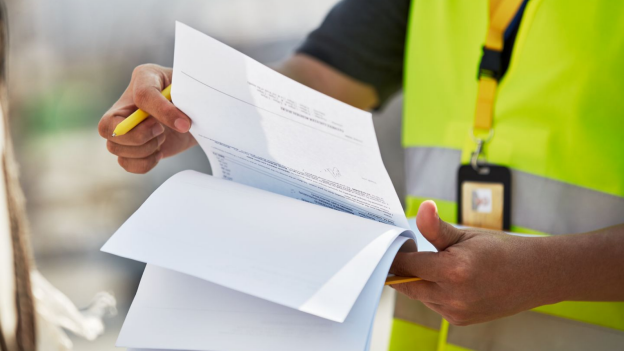
5. Make sure that the liner supplier has the necessary accreditations
I.e. That they can guarantee food safety and reduce the risk of cross-contamination. By following these tips, you can optimize your dry bulk shipping process and ensure the safe and efficient transport of your cargo.
Want to Read More Freight Forwarding Stories?
Get the latest on Air, Ocean and Rail Freight Forwarding in your inbox every month, along with regular invitations to our webinars.