Baycrews: Building the No.1 Logistics Infrastructure in the ‘Select-Shop’ Industry
Summary
Founded in 1977 in Yoyogi, Shibuya-ku in Tokyo, Baycrew’s is a leading ‘select-shop’ company which provides products purchased domestically and abroad alongside its original items.
Since their launch they’ve grown to an organization with over 5,500 employees and almost 500 stores whilst diversifying into a variety of industries such as furniture sales, fitness management and restaurant management.
They have a clear growth strategy based on their corporate mission to ‘provide joy of life through clothing, food, housing and beauty’ and continue to expand their offering. They now operate more than 70 brands and sell their products via their retail stores and online channels.
Customer Challenge
- Inefficient logistics operations across four distribution centers with numerous 3PLs
- Inability to scale up e-commerce deliveries against demand leading to lost sale opportunities
DHL Supply Chain Solution
- Consolidated Baycrew’s existing operations to their Kashiwa-shonan Logistics Centre in Chiba
- Implemented a warehouse management system bringing the retail and e-commerce inventories together
- Setting holistic productivity goals whilst being flexible with resource
- Working with employees to continuously improve
Customer Benefits
- Inbound and outbound capacity almost doubled to 220,000 units daily
- Online sales have more than doubled since the warehouse consolidation
- Enhanced, faster shipping process for online orders
- Service level visibility and improvement through KPI
Customer Challenge
To fulfil their fashion sales, Baycrew’s operated from four warehouses; three for fulfilling retail store orders and one for e-commerce; each operated by different 3PL vendors which brought challenges for both the easy movement of goods and overall stock transparency.
In addition, Baycrew’s e-commerce offering was growing substantially but the warehouse was struggling to scale up its capacity leading to lost sales opportunities.
Baycrew’s recognized their logistics operations were inefficient and after a significant review decided to integrate their multiple sites into a single site, recruiting just one logistics partner to run the high-level operations.
Their goal was to build the number one logistics infrastructure in the industry enabling them to sell their products across all their channels, increasing capacity and supporting their growth plans.
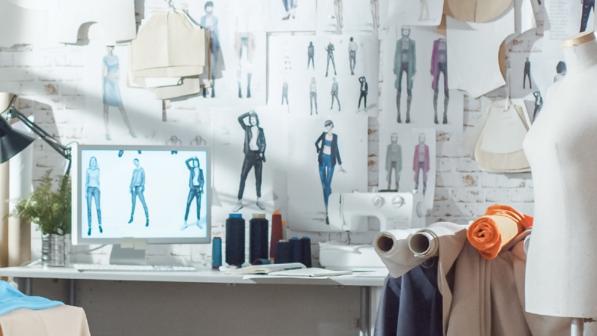
DHL Supply Chain Solution
DHL Supply Chain consolidated Baycrew’s existing operations to their Kashiwa-shonan Logistics Centre in Chiba. The facility is three stories high, has almost 50,000 square meters of space and room for 52 trucks. In addition, it has the benefit of being located just 30 kilometers from Narita and Haneda Airport.
To support Baycrew’s primary requirement DHL Supply Chain implemented a warehouse management system (WMS) bringing the retail and e-commerce inventories together. The WMS was also integrated with Baycrew’s core system to oversee the latest inventory in real time improving efficiency, stock levels and naturally reducing lost sales opportunities.
Using their previous experience DHL Supply Chain recognized the importance of setting holistic productivity goals to create an optimal resource plan. Daily targets such as shipping volumes are posted in visible areas inside the warehouse. Employees are flexibly allocated to a task and when, for example, a delay is identified operators are relocated to support the delayed process.
DHL Supply Chain also advocate employee engagement. Individuals can suggest process improvements within their work area using Kaizen sheets. These are shared across the site and so far, have helped to increase shipping capacity and improve inspection accuracy.
Customer Benefits
Three years have passed since Baycrew’s launched their new logistics site in partnership with DHL Supply Chain. The site has become a critical base delivering omni-channel services everyday through an optimized inventory pool integrating retail and e-commerce stock for fast product delivery.
Consolidation of the multiple sites has helped to build a faster shipping process which better addresses customer needs. The goals of shipping 15,000 orders a day has been achieved and Baycrew’s are looking to grow this to 25,000 within the next one year.
Inbound and outbound capacity has almost doubled from 120,000 items with 3 sites combined to 220,000 with a single site, thanks in part to the WMS accurately capturing both retail and e-commerce orders and allocating accordingly. In addition, new technology used by warehouse operators on their scanners provides instructions as to whether the products need to be shipped right away or stocked.
The center currently stores up to 1.8 million clothing and accessory items. This has addressed the previous issues faced with Baycrew’s online fulfilment, in fact their online sales more than doubled last year (fiscal year ending in August 2018) since the warehouse consolidation and they have outperformed all their peers.
Baycrew’s are now looking at automation and robotics as their next opportunity.