Inventory management plays a vital role in maintaining the delicate balance between supply and demand. For businesses, this balance is critical to avoiding dead stock — inventory that remains unsold and ties up capital — and shortages, which lead to missed sales opportunities and dissatisfied customers. Effective inventory management ensures profitability, enhances customer satisfaction, and streamlines operational efficiency.
This guide outlines actionable strategies to optimize your inventory, helping your business stay ahead in a competitive market.
Strategies for deadstock management
1. Accurate demand forecasting
Demand forecasting in supply chains is fundamental to avoiding excess inventory, as it helps businesses avoid the twin challenges of dead stock and shortages. By analyzing historical sales data, market trends, and seasonality, companies can predict future demand with greater precision.
Advanced tools like artificial intelligence (AI) and machine learning play a transformative role in e-commerce businesses by adding a layer of sophistication to demand forecasting. Collaboration between sales and marketing teams also plays a pivotal role, ensuring inventory levels are aligned with planned promotions, product launches, and broader market shifts.
2. Regular inventory audits
Knowing how to keep track of inventory is essential for maintaining accuracy and avoiding inefficiencies. Regular inventory audits help businesses verify that stock records match actual levels while identifying slow-moving or obsolete items early.
Techniques like cycle counting — where portions of inventory are checked daily — provide a systematic way to monitor inventory without disrupting operations. By implementing these practices, businesses can proactively address issues and optimize stock levels.
3. Just-in-time (JIT) inventory management
The just-in-time approach minimizes excess stock by aligning replenishment with actual customer demand. This method relies on strong supplier relationships to guarantee timely deliveries, reducing storage costs and waste. Lean manufacturing principles further support JIT systems by streamlining production and improving response times to demand changes.
Strategies to prevent shortages
While avoiding excess inventory is critical, ensuring stock availability is equally vital to meet customer demand and maintain service reliability. Here are key techniques for inventory control:
Safety stock levels
Maintaining safety stock levels is a crucial strategy for preventing inventory shortages. By analyzing historical demand variability and accounting for lead time uncertainties, businesses can determine the optimal safety stock levels to meet customer needs consistently. Conducting regular risk assessments helps identify potential supply chain disruptions, such as supplier delays or unexpected demand spikes, and allows businesses to adjust safety stock levels accordingly. Real-time monitoring of inventory levels ensures that safety stock remains adequate in response to changing market conditions.
Inventory management software
Adopting an advanced inventory management system gives businesses unparalleled visibility and control over their inventory. These systems enable real-time tracking of stock levels, movements, and reorder points, reducing the risk of overstocking or stockouts. Data analytics capabilities within the software provide actionable insights, helping businesses identify trends, optimize stock levels, and make informed procurement decisions.
Lead time reduction
Shortening lead times is key to ensuring faster replenishment and minimizing the risk of inventory shortages. Collaborating closely with suppliers to streamline ordering processes and enhance communication can significantly improve delivery timelines. Internally, businesses can identify and address bottlenecks in workflows to accelerate lead times. In some cases, sourcing materials or products locally can further reduce transportation time, ensuring a steady supply of inventory to meet customer demands.
Inventory optimization
Achieving a balanced inventory requires strategic optimization techniques that go beyond basic management practices. Let's explore how targeted approaches can refine inventory processes and maximize efficiency.
1. ABC analysis
ABC analysis is a strategic inventory management technique that segments stock into three categories — A, B, and C — based on their value and significance to the business. Category A includes high-value items that contribute the most to revenue and profitability, often requiring closer monitoring and tighter control. Category B represents moderately valuable items with a balanced demand and cost structure, requiring a more standard level of oversight. Lastly, Category C encompasses low-value items that, while less impactful individually, collectively form a significant portion of inventory volume.
ABC analysis allows businesses to classify inventory based on its value and contribution to profitability. By prioritizing high-value items that have the greatest impact on revenue, companies can allocate resources more effectively. This structured categorization also enables tailored inventory management strategies, ensuring that each category is managed with the appropriate level of attention and oversight to maximize operational efficiency.
2. Demand segmentation
Demand segmentation helps businesses refine their inventory strategies by identifying distinct customer demand patterns based on factors such as seasonality, demographics, and product types. This enables businesses to develop tailored approaches for each segment, optimizing stock levels and replenishment cycles to meet specific needs. Enhanced forecasting accuracy derived from segmentation reduces waste and improves overall inventory efficiency.
3. Multi-echelon inventory optimization
Multi-echelon inventory optimization is a sophisticated approach that considers inventory levels across multiple stages of the supply chain, including suppliers, distribution centers, and retail outlets. By analyzing stock holistically across all tiers, businesses can strategically allocate inventory to the locations where it is most needed, reducing overstocking and minimizing shortages.
For businesses managing complex supply chains, multi-echelon optimization is a game-changing strategy for achieving end-to-end efficiency.
Collaborative Planning, Forecasting, and Replenishment (CPFR)
Collaborative Planning, Forecasting, and Replenishment (CPFR) is a strategic approach that encourages close cooperation between supply chain partners to enhance inventory management. By aligning demand forecasts and inventory plans, businesses, suppliers, and retailers can work in unison to minimize inefficiencies and ensure the smooth turnover of inventory.
- Partner collaboration: Sharing demand forecasts and inventory plans fosters stronger relationships between supply chain partners. This alignment helps suppliers anticipate requirements and ensures retailers maintain optimal stock levels, ultimately leading to a more efficient supply chain.
- Demand visibility: CPFR provides a comprehensive view of demand patterns across the entire supply chain. This visibility empowers businesses to make data-driven decisions, accurately predict demand, and avoid both stockouts and excess inventory.
- Reducing the bullwhip effect: The bullwhip effect occurs when small demand fluctuations at the consumer level become amplified as they move up the supply chain. CPFR mitigates this issue by improving communication and coordination among supply chain partners, ensuring a more stable and responsive inventory system.
Take control of your inventory with smart strategies and DHL Express
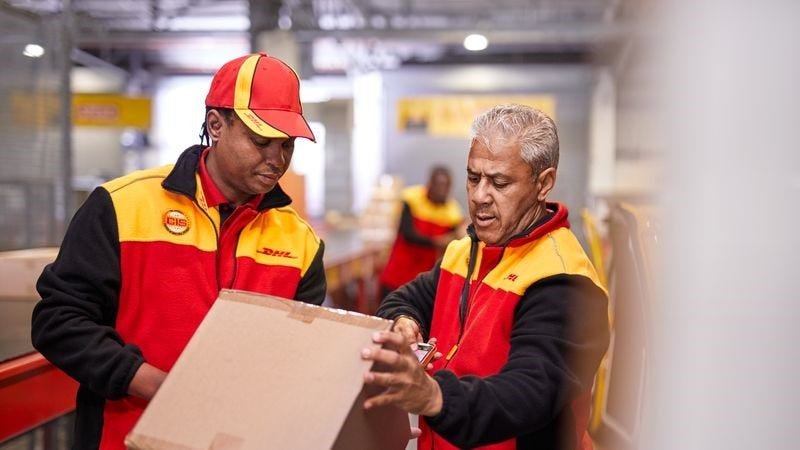
Effective inventory management is critical for maintaining a balance between supply and demand while avoiding the pitfalls of dead stock and shortages. By implementing strategies such as accurate demand forecasting, regular inventory audits, and advanced inventory management systems, businesses can ensure supply chain agility and respond effectively to market changes.
Achieving this level of control often requires leveraging the right tools and partnerships. Utilizing inventory tracking systems and integrated software not only streamlines planning and operations but also enhances synergy across supply chain functions. This results in improved efficiency, higher customer satisfaction, and stronger profit margins.
Partnering with an international logistics provider like DHL Express can further enhance your inventory management capabilities. With advanced tracking and monitoring features, shipment visibility, and tailored shipping solutions, DHL helps businesses maintain better control over their inventory and improve customer experiences.
If you're ready to elevate your inventory management practices and shipping efficiency, consider opening a DHL Express business account today and experience the benefits of a seamless, technology-driven logistics solution.