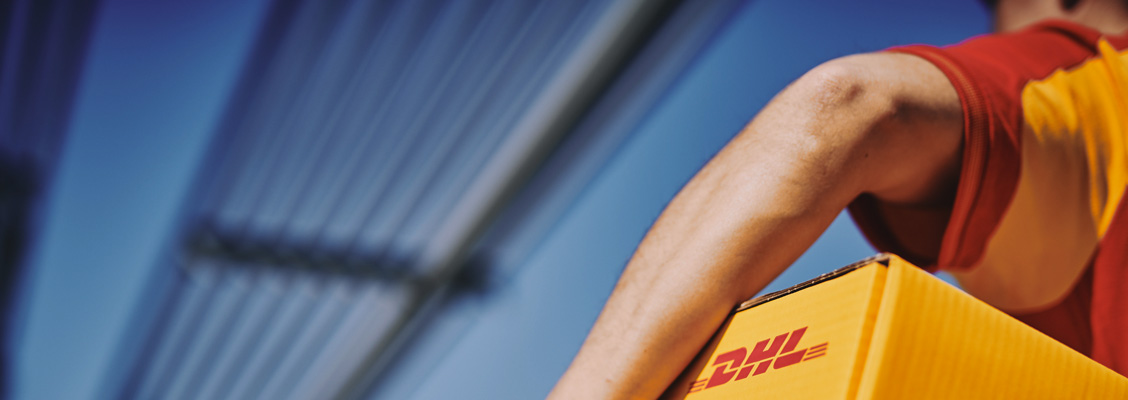
In an era where convenience and speed are not just valued but expected, e-commerce shipping is undergoing a significant transformation. The rapid growth of online shopping has escalated consumer demand for faster, more reliable last-mile delivery options, pushing the boundaries of what traditional logistics networks can provide.Â
To meet these evolving demands, logistics providers have turned to artificial intelligence (AI) as a pivotal tool to revolutionise the last-mile delivery process. In this article, we explore the benefits of AI in logistics and transportation, how it contributes to a more efficient supply chain and how AI logistics enhances the overall customer experience.
Last-mile delivery: The linchpin of e-commerce success
Last-mile delivery is the critical final step that connects products with their final recipients and is heavily linked to customer satisfaction. This connection stems from the immediate impact timely and accurate deliveries have on the consumer experience – prompt e-commerce shipping delivery times and the condition of the received goods significantly influence a customer's perception of a brand. According to a study from the Journal of Mathematical Methods and Analysis for Industrial Management and Business, there is a direct correlation between the efficiency of last-mile delivery and increased customer satisfaction, with businesses reporting higher retention rates and loyalty among customers who receive their purchases quickly and reliably.
Besides the delivery experience, today’s consumers are also increasingly concerned about the sustainability of last-mile delivery methods. The environmental footprint of these operations, highlighted by the carbon emissions of delivery vehicles and poor route optimisation leading to increased fuel use, is under growing scrutiny from both consumers and businesses. This heightened awareness has led to a demand for brands to adopt greener and more efficient practices into their last-mile e-commerce shipping strategies, such as AI logistics, understanding that ecological responsibility goes hand in hand with fulfilling customer expectations and fostering a positive brand image.
Challenges of traditional last-mile delivery methods
Traditional last-mile delivery methods are quickly becoming ineffective in the evolving e-commerce landscape. These are some of the challenges faced:
- Poor route optimisation:Â Traditional last-mile delivery models often do not incorporate route optimisation due to a lack of advanced technological tools and data analytics capabilities, making it difficult to dynamically adjust routes based on real-time traffic conditions, delivery urgencies, and other critical factors.Â
- Trouble scaling operations during peak demand:Â Traditional last-mile delivery models rely on fixed resources and infrastructure that cannot be quickly adjusted or expanded to match sudden increases in demand. These include pre-set routes, a limited fleet of vehicles, and a workforce sized for average demand levels.Â
- A growing gap between consumer expectations and logistic capabilities:Â Today's consumers demand features such as real-time tracking, the ability to choose delivery times, and even options for environmentally friendly delivery methods. Traditional last-mile delivery systems, often rigid and lacking in technological integration, find it challenging to meet these multifaceted demands.
How AI is transforming logistics and last-mile delivery
The use of AI in transportation, last-mile delivery and throughout the supply chain has ushered in a new era for logistics, tackling age-old inefficiencies with cutting-edge solutions. Here are some benefits of AI in logistics:
- AI-driven route optimisation: AI machine learning algorithms analyse vast amounts of data, including traffic patterns, weather conditions, and delivery urgencies, to devise the most efficient delivery paths in real time. This not only shortens delivery times but also reduces fuel consumption, directly impacting both operational efficiency and environmental sustainability.
- Demand forecasting: AI plays a pivotal role in predicting future order volumes, allowing logistics providers and e-commerce businesses to better manage inventory and warehouse operations. By analysing historical data, AI can forecast demand trends, enabling companies to optimise stock levels and reduce waste.Â
By optimising routes and improving demand forecasting, AI-powered logistics and supply chains greatly reduces the number of vehicles on the road and the distance travelled, significantly lowering emissions.Â
How DHL Express is integrating AI into our last-mile delivery
DHL Express is at the forefront of implementing AI into our logistics operations, improving the way we conduct e-commerce shipping and last-mile delivery in Singapore.
AI-powered last-mile delivery route optimisationÂ
Using AI-powered logistics software, DHL Express optimises last-mile delivery by analysing data with up to 95% certainty on incoming shipping volumes, enabling precise planning of courier routes based on variables like volume and service requirements. This optimisation continues within the delivery vehicle, where AI software arranges stops, prioritising urgent deliveries or specific time requirements.Â
This is all complemented by DHL Express's Follow My Parcel feature providing customers with real-time delivery updates, offering flexibility for delivery adjustments, enhancing customer satisfaction and improving first-attempt last-mile delivery rates.Â
Using AI to improve vehicle fuel efficiency
DHL Express also leverages AI in transportation to improve fuel efficiency across our last-mile delivery fleet. Besides route optimisation to minimise time spent in transit, AI analytics are employed to detect inefficiencies, such as excessive idling or suboptimal loading processes, further driving fuel and operational efficiencies.
AI-powered sorting with DHLBot
Installed in the DHL Express sorting hub in Singapore, the DHLBot is an AI-powered robotic arm which automates the parcel sortation process, complementing the manual sortation done by workings and enabling delivery hubs to handle greater volumes. It is able to sort over 1,000 small parcels an hour with 99% accuracy, reducing the probability of mis-sorting and increasing overall operational efficiency by 40%.
How it works:Â
The DHLBot uses AI algorithms to greatly improve the speed and efficiency of parcel sorting during shipping, addressing one of the key bottlenecks during the last-mile delivery phase. 3D and barcode cameras scan the airway bill on each package for its targeted destination as it travels through the conveyor belt before the DHLBot sorts them into their respective delivery bins.
Benefits and results:
The DHLBot has dramatically improved DHL Express's operational capabilities, allowing for quicker processing times and acting as “additional manpower” during peak season last-mile delivery surges. Furthermore, by automating routine sortation tasks, the bot frees up DHL Express employees to focus on more complex and strategic work, enhancing productivity and job satisfaction. Last but not least, the efficiency and accuracy brought by the DHLBot contribute directly to faster delivery times and reduced e-commerce shipping errors, leading to higher customer satisfaction rates.